OUTFEED TRAINING
Introduction to the Outfeed
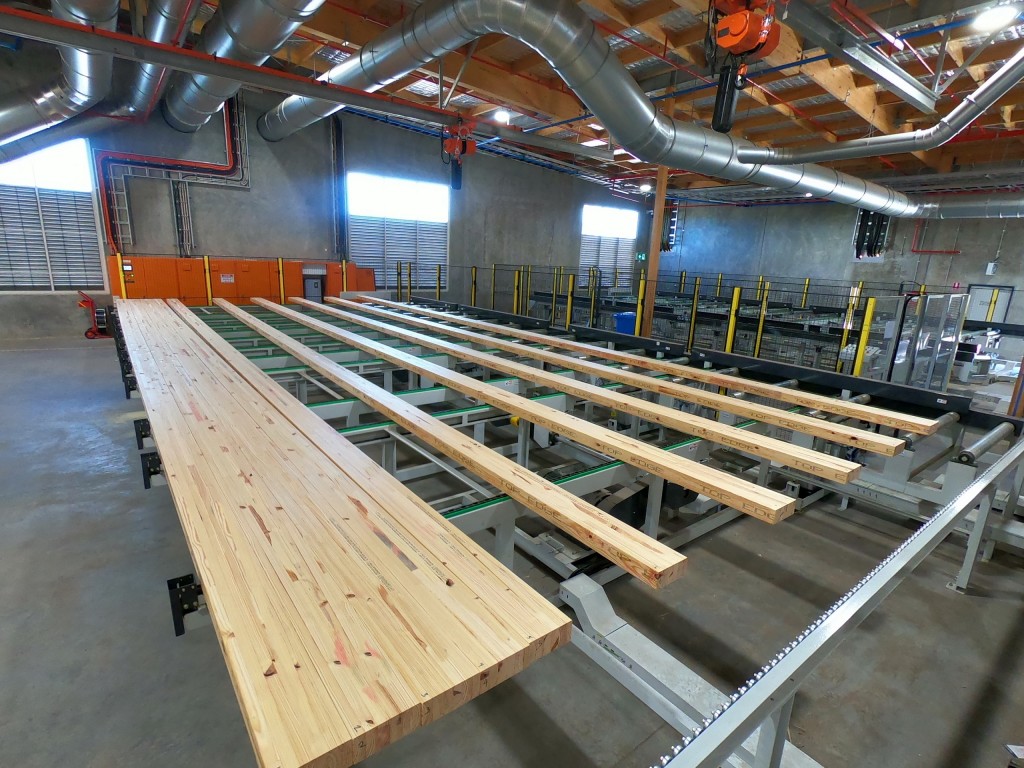
Introduction
The Outfeed Station plays a crucial role as the final stage in the Glulam production process. It is responsible for receiving finished beams from the finishing planer, inspecting them for quality, packaging them for storage or shipment, and applying necessary tags for traceability. This module will provide a comprehensive introduction to the function and importance of the outfeed station, as well as an overview of the equipment used and the key components of the workstation.
The outfeed station ensures that only high-quality beams that meet production standards are packaged and sent for distribution. Maintaining consistency, quality, and operational efficiency at this stage is essential to the overall production process. Proper handling, inspection, and management of beams are vital to ensuring that the finished products meet customer specifications and company standards.
Key Responsibilities
The outfeed station plays a pivotal role in the overall production process by:
- Receiving Beams: The outfeed station receives finished beams from the finishing planer and moves them onto the outfeed conveyor for inspection and packaging.
- Inspecting Beams for Defects: Each beam is inspected for quality and defects such as glue lines, clamp marks, wane, and other surface issues. Beams that meet quality standards are moved forward for packaging.
- Packaging Beams: Beams are securely bundled and strapped using a strapping machine to ensure they are safe for transportation.
- Tagging and Tracking Beams: Each pack of beams is tagged using the ADF system, ensuring proper identification and traceability within the production and distribution chain.
- Storing Packs: Completed packs are stored in designated areas, ready for dispatch or further processing. Proper storage is crucial to maintaining beam quality and organization within the warehouse.
The outfeed station ensures that only beams meeting the required quality standards are shipped out, contributing to the overall product quality and customer satisfaction.
Key Components of the Outfeed
Outfeed Conveyor System:
- Function: The outfeed conveyor system transports beams from the finishing planer to the inspection and packaging areas. It allows for smooth and controlled movement of the beams, ensuring no damage occurs during this transition.
- Importance: Keeping the conveyor in good working order is essential for avoiding bottlenecks in the production process. Regular maintenance and monitoring of the system ensure its smooth operation.
Overhead Cranes:
- Function: Overhead cranes are used to lift and move beams from the outfeed conveyor to inspection areas and then onto packaging.
- Importance: The overhead crane allows for efficient handling of large, heavy beams, minimizing the need for manual labor and reducing the risk of injury. Proper crane operation is essential for ensuring beams are not damaged during movement.
Saw Horses:
- Function: Saw horses provide a stable surface for placing beams during inspection. This allows operators to conduct quality checks and apply tags easily.
- Importance: Stability during inspection is crucial to detecting any defects or damage in the beams. Proper use of saw horses ensures that beams are handled safely and efficiently.
Strapping Machines:
- Function: The strapping machine secures beams into packs by tightly strapping them together for easy handling and storage.
- Importance: Ensuring beams are securely strapped is key to avoiding damage during transportation or storage. Strapping machines must be properly maintained to function effectively.
Label Printer (ADF System)
- Function: The ADF (Automated Data Flow) system is used to generate tags for each pack of beams, providing information such as beam size, type, and production details.
- Importance: Tagging is essential for maintaining traceability throughout the supply chain. Proper use of the ADF system ensures that all packs are correctly identified and tracked during storage and shipping.
Storage Racks
Overview of Training Modules
This training module is the first step in a comprehensive learning experience designed to equip you with the knowledge and skills required to safely and efficiently operate the outfeed station. The following modules will build on the foundation provided here, covering detailed operational procedures, safety guidelines, and troubleshooting techniques.
-
Module 2: Safety and Emergency Procedures – You will learn about the specific safety protocols, personal protective equipment (PPE), and emergency stop (E-stop) locations for the outfeed station. Safety is a top priority, and understanding the correct procedures will ensure your safety and the safety of others.
-
Module 3: Pre-Operational Checklist – This module covers the detailed steps that need to be taken before starting the outfeed station. From verifying that all components are functional to checking the tag printer, pre-operational checks are vital to ensuring that everything is ready for a smooth and efficient shift.
-
Module 4: Operating the Outfeed Station – In this module, you will learn how to operate the outfeed conveyor, inspect beams for quality, and handle packaging. The module also covers adjusting conveyor speed and managing the movement of beams throughout the process.
-
Module 5: Printing ADF Tags and Allocating Packs – Here, you will learn how to use the ADF system to print labels and allocate packs. Proper management of tags ensures that all packs are correctly identified, facilitating easy tracking and inventory management.
-
Module 6: Downtime Management – Downtime is inevitable in any production environment. This module teaches you how to make the most of downtime by performing maintenance tasks, cleaning the workstation, and ensuring that all tools are in place.
-
Module 8: End-of-Shift Procedures – At the end of each shift, it’s important to properly shut down and clean the equipment. This module will walk you through the necessary steps to ensure the outfeed station is ready for the next shift.
-
Module 10: Verification of Competency – The final module will assess your knowledge and competency through a series of practical and theoretical tests. Once you have demonstrated your ability to operate the outfeed station independently, your supervisor will sign off on your competency.
By the end of Module 1, you will have a solid understanding of the outfeed station’s purpose, the key components involved, and what to expect from the following training modules. This foundational knowledge is crucial to your success as an outfeed operator, setting you up for safe and effective operation in future lessons.