OUTFEED TRAINING
Operating the Outfeed
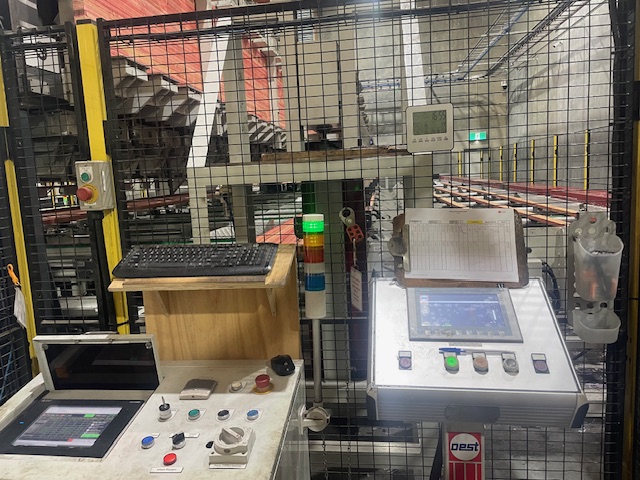
Introduction
Operating the Outfeed section is the final stage of production and requires precision, attention to detail, and adherence to safety and quality standards. At this point, finished beams are handled, inspected, packaged, and prepared for shipment. The main goals are to ensure that all beams meet the required specifications, are securely packaged, and are correctly stored or dispatched.
Receiving Beams from the Finishing Planer
The first step in operating the Outfeed is to correctly receive the beams from the finishing planer. This task sets the foundation for the rest of the process, as improper handling at this stage can lead to production inefficiencies or product damage.
Key Responsibilities
-
Placement: The crew operating the finishing planer will place beams onto the Bottom End skids. Your job is to ensure the beams are positioned properly on the Outfeed rollers or skids for easy handling and inspection.
-
Organized Setup: Ensure that beams are laid out in an organized manner for smooth transition into the inspection phase. If beams are misaligned or disorganized, it could lead to delays in the production flow.
Tools and Equipment Used
-
Outfeed Rollers: These rollers move the beams from the finishing planer to the inspection area. Ensure they are clean and free from debris to avoid obstruction.
-
Overhead Crane: For larger or heavier beams, use the overhead crane to lift and move them to saw horses for inspection. Follow all safety guidelines in the crane operation manual.
Inspecting Beams
Inspection is a critical step in the Outfeed process to ensure the beams meet all quality specifications. This includes checking for defects, measuring dimensions, and ensuring that each beam is structurally sound before it is packaged for delivery.
Key Responsibilities
- Measurement and Assessment: Place the beams on saw horses to provide a stable inspection platform. Use the company’s quality checklist to assess each beam for the following:
- Correct Size: Verify the beam’s dimensions, including length, width, and thickness, to ensure they match the order specifications.
- Camber: Ensure the beam has the correct curvature, as required by the product’s specifications.
- Defects: Identify any defects that may affect the beam’s quality. These may include depressions, holes, or other visual inconsistencies.
- Common Defects to Check:
- Depressed Laminates: Laminates with unacceptable levels of depression should be flagged. Refer to the company’s guidelines on allowable depression based on beam size.
- Want and Wane: Check for the presence of this defect, which occurs when the edges of the timber are incomplete or uneven. Minor defects under 10mm are acceptable; otherwise, notify a supervisor.
- Holes in the Beam: Check for small holes caused by stepped finger joints. Holes under 5mm wide and 100mm long may be acceptable if filled with epoxy; otherwise, notify a supervisor.
- Clamp Depressions: Small clamp depressions under 3mm are acceptable, but anything larger requires supervisor approval.
Tagging for Packaging
Once a beam passes inspection:
- Print the ADF Tag: After inspection, generate a tag through the Automatic Data Feed (ADF) system. The tag contains essential information, including beam size, grade, and destination.
- Attach the Tag: Ensure that the tag is securely attached to the beam for identification during the packaging and storage process.
Packaging Beams
After inspection, the beams must be securely packaged for storage and transportation. Proper packaging prevents damage during transit and ensures that beams can be easily identified and handled.
Key Responsibilities
-
Pack Formation: Stack beams that are of the same size and length together. Alignment is critical to maintaining the stability of the pack. Ensure that the beams are stacked neatly, with the top edges aligned and the ends squared.
-
Strapping the Pack: Use the strapping machine to securely bind the beams together into stable packs. The strapping ensures that beams don’t shift during transport or storage, which could cause damage or misalignment.
-
Dunnage Placement: Dunnage, or spacers, must be placed between layers of beams to prevent shifting and to allow cranes or forklifts to lift the packs safely. Follow the company’s guidelines for proper dunnage placement.
-
Labeling the Pack: Once the pack is formed and strapped, write the pack number on the side for easy identification in case the ADF tag is lost or damaged. This is crucial for tracking during storage and dispatch.
Tools and Equipment Used
- Strapping Machine: This machine is used to apply durable straps that secure the beams into cohesive packs.
- Dunnage Materials: Ensure that the dunnage is the correct size and properly placed according to the packaging guidelines.
Storing Packs
Proper storage of the finished beam packs is essential for maintaining order in the storage area and ensuring that products are easily accessible when preparing them for shipment.
Key Responsibilities
- Designated Storage Areas: Follow specific guidelines for where each type of pack should be stored:
- Impianti Storage Bay: Used for packs of 65mm beams that are 6.6 meters and shorter, as well as LGL packs up to 8.7 meters.
- Bottom End Storage: Reserved for pine beams that are not destined for the Top Shed or Chop Shop.
- Chop Shop Storage: Hardwood Tasmanian Oak and large pine beams are stored here. Always ensure packs are stored with their top edges facing the southern side of the shed.
- Storage Orientation: The orientation of the packs is critical to maintaining accessibility and preventing product confusion. Proper orientation helps with crane handling and makes loading for dispatch more efficient.
Cutting and Repackaging Single Beams
Sometimes beams may not meet the required length, or they may need to be repurposed based on customer specifications. When this happens, beams will need to be cut and repackaged.
Key Responsibilities
-
Quality Check and Tagging: Before cutting, place the beam on saw horses and perform the same quality checks as outlined in the inspection process. Once the beam passes inspection, ensure that it is correctly tagged with the new information before proceeding with the cut.
-
Using the Cutting Solutions Sheet: Refer to the cutting solutions sheet, which provides the optimal lengths to cut beams into for repurposing. This sheet is designed to maximize the usability of the beams and reduce waste.
-
Repackaging: After the beams have been cut, follow the standard packaging process to repackage them into secure packs. Ensure that each pack is properly tagged and stored in the designated area.