OUTFEED TRAINING
Printing ADF Tags
Introduction
The ADF (Automatic Data Feed) system is an essential tool in the Outfeed section, used for generating, printing, and managing labels for beam packs. These labels contain crucial information such as the size, grade, and destination of the beams, which is necessary for tracking the beams throughout the storage and dispatch process. Accurate and consistent labeling ensures that all beams are properly identified, reducing errors in inventory and shipping.
This lesson will guide operators through the step-by-step process of using the ADF system to print, allocate, and manage pack tags.
Understanding the ADF System
The ADF system is a computerized interface that allows operators to input key information about each beam pack and generate tags that can be affixed to the pack. The system’s touch screen interface streamlines the process, ensuring ease of use and reducing the risk of human error.
Key Features of the ADF System
- Touch Screen Interface: The user-friendly interface allows operators to input data easily and navigate through different options.
- Label Preview: Before printing, operators can review the label information to ensure it is correct. This helps prevent printing mistakes that could lead to tagging errors.
- Pack Management: The system provides options for allocating packs, converting pack details, and managing reprinting needs.
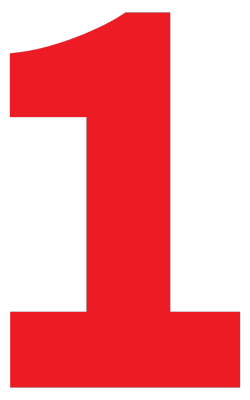
Accessing the ADF System
Logging In
To begin the label printing process, the operator needs to log into the ADF system:
- Operator Selection: Select your name from the drop-down list on the login screen. This ensures that the system tracks which operator is generating the tags and maintains accountability.
Navigating to the Out Screen
Once logged in, navigate to the Out Screen:
- Out Panel: This is the primary screen used for printing labels. Ensure that all selections and data entries are made on this screen for consistency and accuracy.
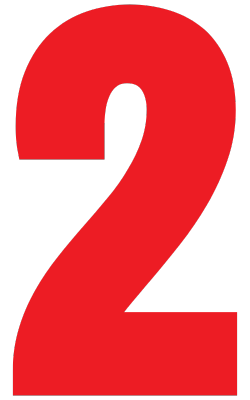
Entering Pack Information
Profile Selection
In the Profile section, you will need to enter specific details about the pack. These details are critical for generating accurate labels that reflect the beam specifications and ensure proper identification.
-
Profile: Select the appropriate profile for the pack from the dropdown menu. This will typically include general information about the type of product being processed.
-
Species: Choose the species of timber from the available options (e.g., Pine, Tasmanian Oak). This ensures that the label accurately reflects the type of timber in the pack.
-
Seasoning: Select the seasoning status of the timber (e.g., Kiln-Dried or Green). Proper seasoning identification is important for maintaining product integrity during storage and transport.
-
Width and Depth: Enter the width and depth of the beams. These dimensions must match the specifications of the product being packaged.
-
Grade: Choose the grade of the timber from the options provided. Timber grades are used to categorize beams based on their strength, durability, and suitability for different applications.
-
Length: Enter the length of the beams in the pack. If a non-standard length is required, use the Dock to Length (DTL) option to manually enter the specific length. This flexibility allows you to account for custom orders or specific customer requirements.
-
Tallies: Input the number of pieces in the pack using the number pad or the plus/minus buttons on the screen. Ensure that the tally reflects the exact number of beams in the pack.
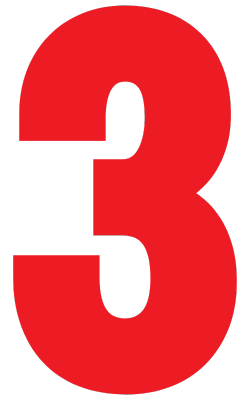
Setting the Destination and Storage Location
Once the pack information has been entered, you will need to set the destination and storage location for the pack. This ensures that the beams are correctly routed through the facility and prepared for shipment.
-
Destination: Select the destination of the pack, which may refer to the final customer or a storage location within the facility. Ensuring the correct destination is crucial for accurate dispatch.
-
Bin Location: Choose the bin location where the pack will be stored before shipment. This is an important step in keeping the storage area organized and ensuring that packs can be easily retrieved when needed.
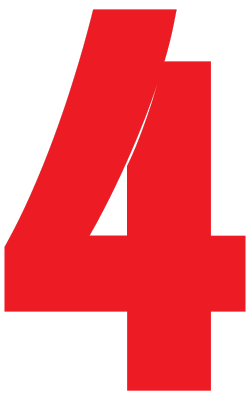
Previewing and Printing the Label
Lay-Up Date
Before printing the label, enter the Lay-Up Date, which reflects when the beams were manufactured or prepared. This is important for tracking product age and ensuring that older packs are used first in dispatch.
Previewing the Label
After all data is entered, the system provides a preview of the label:
- Label Preview: Carefully review the label preview on the screen. Check that all information (dimensions, species, grade, etc.) is correct. You can enlarge the preview by touching and holding the label to ensure clarity.
Printing the Label
Once you’ve verified that the label is correct:
- Press ‘GO’: If the status bar shows “Ready to Process” in green, press the ‘GO’ button to print the label.
If you need to print multiple labels, you can modify the necessary fields or press ‘CLR’ to start a new entry. Ensure that each label corresponds accurately to its pack to avoid confusion.
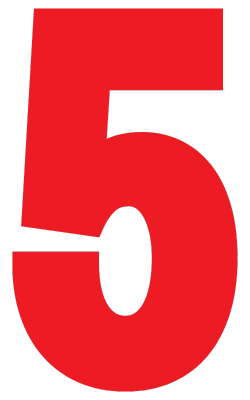
Managing Packs
Allocating Packs
Once a pack has been labeled, it needs to be properly allocated within the system. Allocation ensures that the pack is recorded with its specific destination and storage location for inventory tracking.
- Select the Pack: From the list on the Out Screen, choose the pack that has just been labeled.
- Destination and Bin Location: Verify or update the destination and bin location.
- Press ‘GO’: Confirm the allocation by pressing the ‘GO’ button. This step ensures the pack is routed correctly within the system and can be easily tracked.
Cancelling Incorrect Packs
If an error is made during label generation, you can cancel the pack to prevent mistakes in inventory and dispatch.
- Navigate to the Incorrect Pack: On the Out Screen, select the pack that needs to be cancelled.
- Press ‘CLR’: This will clear the incorrect pack entry. Ensure that the status bar shows a green “Cancelled” message to confirm that the pack has been removed from the system.
Converting Packs
Sometimes, specifications for a pack may change, such as its length, grade, or destination. In such cases, the pack needs to be converted within the system to reflect the new specifications.
- Select the Pack: Choose the pack that requires conversion.
- Modify Specifications: Update the necessary fields (e.g., length, grade).
- Press ‘GO’: Once changes are made, press the ‘GO’ button to finalize the new details and generate a new label, if required.
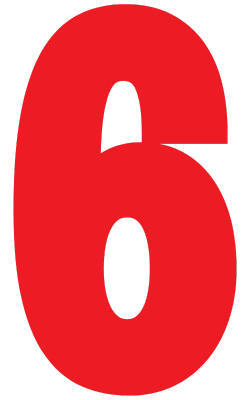
Using the ADF Cutting Screen
Overview
The ADF Cutting Screen is used when packs need to be resized or repurposed. This may occur when beams don’t meet customer specifications or when an order requires beams of different lengths.
- Navigate to the Cutting Screen: From the ADF system’s main menu, access the Cutting Screen.
- Select the Pack: Choose the pack that needs to be resized.
- Enter Cutting Instructions: Input the desired lengths and the number of pieces required. Ensure that the cutting instructions align with customer specifications or internal requirements.
- Preview and Confirm: Review the cutting instructions on the screen and press ‘GO’ to update the pack information.
This step ensures that the beams are properly prepared for cutting and that the system reflects the new specifications.
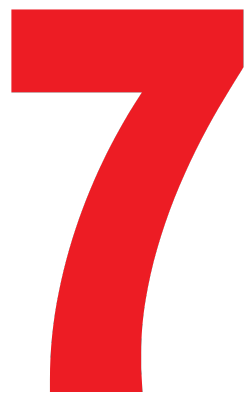
Reprinting Pack Tags
Overview
In the event that a pack tag is lost, damaged, or printed incorrectly, it is possible to reprint the tag without recreating the entire pack in the system. Reprinting tags ensures that each pack is properly identified and tracked.
- Access the Reprint Screen: Navigate to the Reprint Screen from the ADF system’s main menu.
- Select the Entry Date: Choose the date the pack was originally created to narrow down the list of packs.
- Select the Pack Number: From the list, select the correct pack number for which you need to reprint the tag.
- Press ‘GO’: Review the tag preview and press ‘GO’ to reprint the label.
Well Done!
- Proper usage of the ADF system is essential for maintaining an organized inventory, ensuring the accuracy of orders, and avoiding costly errors in the dispatch process.