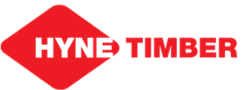
ROTARY PRESS TRAINING
Introduction to the Rotary Press
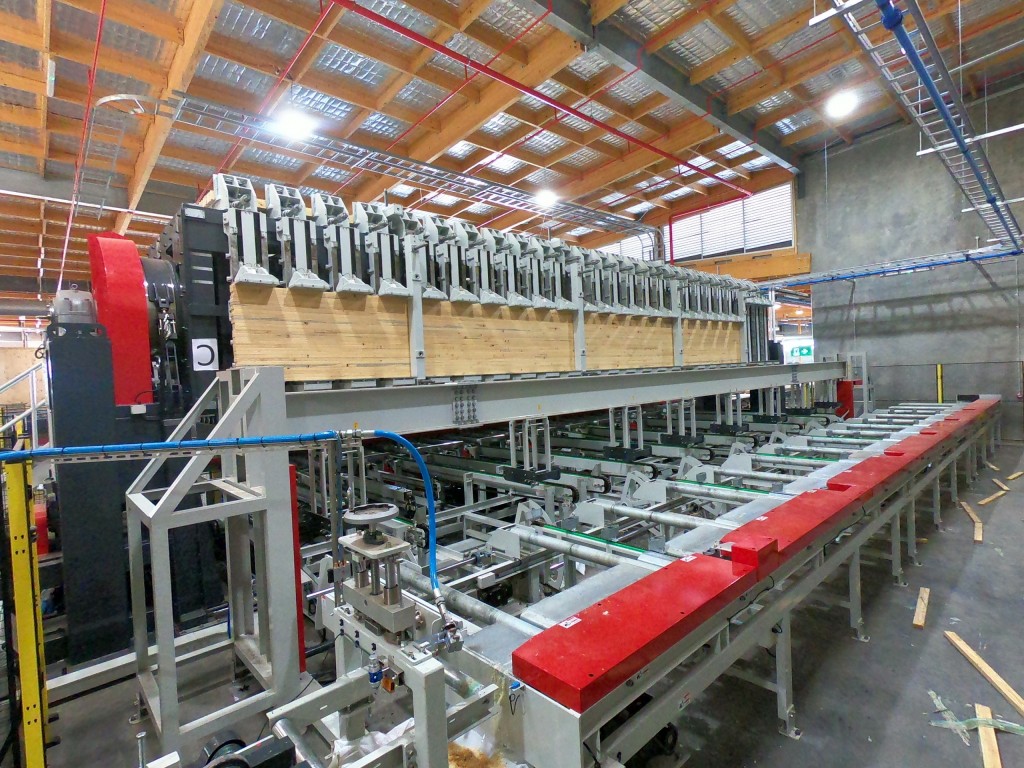
Course Menu
- Back to Main Menu
- Lesson 1 – Introduction
- Lesson 2 – Safety Procedures
- Lesson 3 – Pre-Operational Checks
- Lesson 4 – Operating Instructions
- Lesson 5 – Glue Test
- Lesson 6 – Size Change
- Lesson 7 – Troubleshooting
- Lesson 8 – When Down,Do
- Lesson 9 – End of Shift Procedures
- Lesson 10 – Competency Quiz
- Lesson 11 – Trainer Verification
Introduction
The Rotary Press is a vital component in the production of laminated beams at our facility. This module will provide you with an essential understanding of the Rotary Press, its purpose, key components, and an overview of the training modules that will guide you through its operation, safety protocols, and maintenance procedures. Mastery of this equipment is crucial for ensuring the consistent quality and efficiency of our production process.
Purpose of the Rotary Press
The primary purpose of the Rotary Press is to automate the layup, clamping, and curing processes required to produce high-quality Glulam beams. This equipment ensures that the beams are pressed to the required specifications and standards before being transferred to the finishing planer for dressing. By automating these critical steps, the Rotary Press significantly enhances production efficiency while maintaining stringent quality control.
Key Components
Rotary Press:
The Rotary Press is the core component of the workstation. It applies the necessary pressure to laminated beams, ensuring the adhesive bonds the layers together securely. This step is critical in producing high-quality beams that meet structural and safety standards. Consistent and proper operation of the rotary press is essential for maintaining product integrity, and any malfunctions can result in defects or production delays.
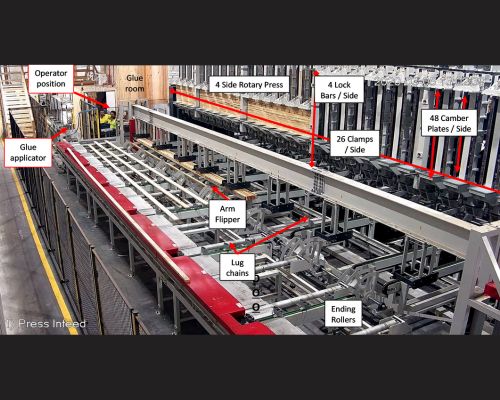
HMI Control Panel
The HMI Control Panel (Human-Machine Interface) is the main control system for the rotary press. It allows operators to monitor the press’s operation, adjust key settings such as pressure levels and cycle times, and respond to any alerts or issues in real-time. The control panel plays a crucial role in ensuring the press runs safely and efficiently, providing the operator with full oversight of the pressing process.
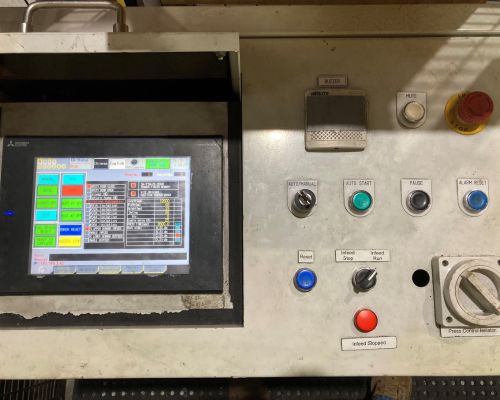
Glue Applicator:
The Glue Applicator is responsible for dispensing adhesive onto the beams before they enter the press. Accurate glue application is critical to the integrity of the final product. Regular cleaning and calibration of the applicator are necessary to avoid defects such as weak bonds or uneven surfaces. Ensuring proper glue distribution directly impacts the strength and quality of the beams produced.
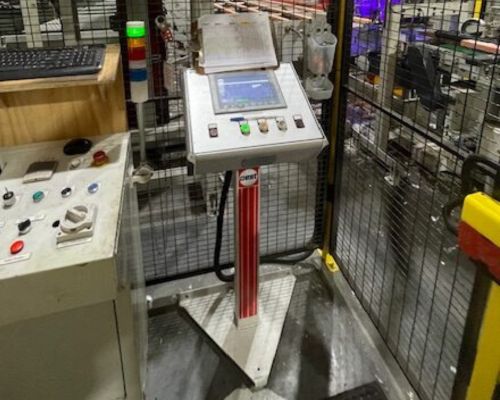
Glue Room:
The Glue Room houses the adhesives used during the pressing process and supports the glue application system. The conditions in the glue room, such as temperature and humidity, must be maintained at optimal levels to ensure the adhesive maintains the correct viscosity.
The glue room is temperature controlled to approximately 30 degrees to aid suitable glue handling and application for a quality glue bond. Refer to the current Safety Data Sheet (SDS) for each chemical before using it. Check the glue is not past its expiry date. Changing over glue IBC’s is part of the forklift operator’s duties to be assisted by the rotary press operator.
Glue IBC Valve Tap
The glue pipe to the glue pump below is gravity fed. The valves are shown open – turn 90 degrees to close.
Glue Room Roller Door
The control to open or close the glue room roller door is accessed on the floor level to the right of the roller door. Close the roller door before entering the glue room to remove a fall hazard.
Glue
The PUR 681.xx glue IBC is put in the glue room by the forklift. Ensure no-one is in the room unless a SWMS / Take 5 has been done to control the risk of forklift / pedestrian contact or falling out the roller door.
Glue Release
Decant the 901.10 release agent from the 20 litre drum into smaller containers in the glue room. Use rags or sawdust to clean up spills.
Glue Pump
The pump is beside the glue room downstairs. The control panel is at the operator position to control glue flow rate.
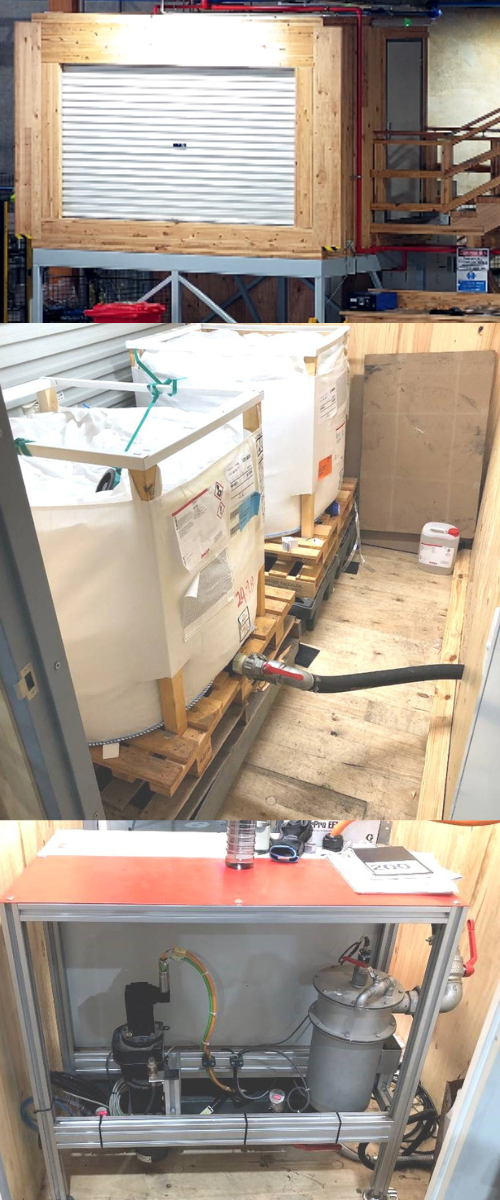
Glue Cleaning Station
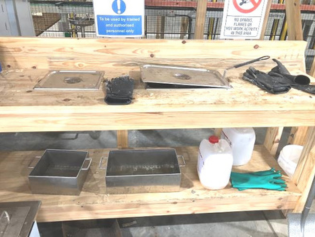
Cleaning Station
The glue cleaning station is in front of the stairs to the press glue room. This is a hazardous area with various hazardous chemicals in use and should be kept clean and clear of unnecessary personnel.
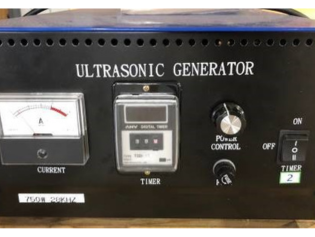
Ultrasonic Generator
The work bench has all the tools and equipment needed to remove glue build up and keep the plant running as it should. Maintain tools and PPE in good condition and return to correct storage after use.
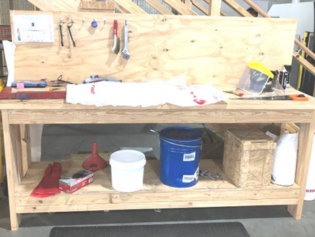
Work Bench
The work bench has all the tools and equipment needed to remove glue build up and keep the plant running as it should. Maintain tools and PPE in good condition and return to correct storage after use.
Hazardous Chemicals
- When using the Glue Cleaning Station, Refer to the Safety Data Sheets for each chemical before use to ensure suitable PPE and procedures are used.
- Never drop items into chemicals in a way that causes splashes
- Ensure all chemical containers are correctly labelled and safe to us
Overview of Training Modules
This training program is designed to equip you with the knowledge and skills necessary to operate the Rotary Press safely and effectively. The modules are structured as follows:
Lesson 2 – Safety Procedures:
Learn critical safety protocols, including proper PPE use, E-Stop buttons, and isolation gates to ensure a safe work environment.
Lesson 3 – Pre-Operational Checks:
Understand how to inspect key components, check glue levels, and complete setup tasks before starting the press.
Lesson 4 – Operating Instructions:
Step-by-step guide on starting, monitoring, and adjusting the rotary press for smooth and efficient production.
Lesson 5 – Glue Test:
Learn how to perform a glue test and verify correct adhesive application for optimal bonding.
Lesson 6 – Size Change:
Discover how to adjust the press for different beam sizes while maintaining production quality.
Lesson 7 – Troubleshooting:
Identify and resolve common issues, handle error codes, and perform manual operations when needed.
Lesson 8 – Press Plate Change:
Understand the process for safely changing press plates to prepare for different production runs or maintenance.
Lesson 9 – When Down, Do:
Learn routine tasks to complete during downtime, including cleaning, checking tools, and maintenance.
Lesson 10 – End of Shift Procedures:
Proper shutdown and cleaning steps to ensure the station is ready for the next shift.
Lesson 11 – Competency Quiz:
Test your knowledge and verify your competency in operating the rotary press safely and efficiently.
By the end of this training, you will have a comprehensive understanding of the Rotary Press and be well-prepared to operate it safely and efficiently, contributing to the overall success of our production process. Let’s get started and make safety and quality our top priorities.