ROTARY PRESS TRAINING
Operating the Press
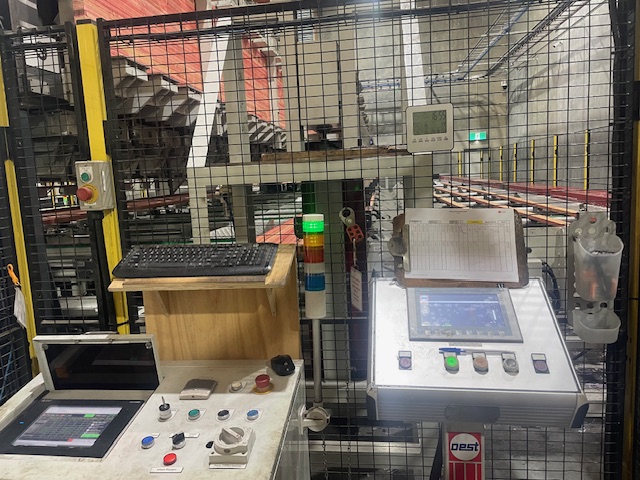
Course Menu
- Back to Main Menu
- Lesson 1 – Introduction
- Lesson 2 – Safety Procedures
- Lesson 3 – Pre-Operational Checks
- Lesson 4 – Operating Instructions
- Lesson 5 – Glue Test
- Lesson 6 – Size Change
- Lesson 7 – Troubleshooting
- Lesson 8 – When Down,Do
- Lesson 9 – End of Shift Procedures
- Lesson 10 – Competency Quiz
- Lesson 11 – Trainer Verification
Introduction
The rotary press is a critical component of our production process, designed to press and bond timber laminates using a high-pressure system. This module will provide an overview of the key components involved in the operation of the rotary press, focusing on the glue system, safety features, and the steps involved in producing high-quality laminated beams. By understanding these components, you will be better equipped to operate the machine safely and efficiently.
Rotary Press
The rotary press is the central machine that compresses timber laminates under high pressure, bonding them together to form structurally sound beams. The press operates using multiple hydraulic vices that apply uniform pressure across the laminate surface to ensure strong adhesion.
Press HMI Overview
The HMI control panel is the user interface for the rotary press. Operators use this panel to manage all aspects of the press operation (excluding glue settings). It also displays data on the current press, error codes and provides access to the manual mode for troubleshooting. The HMI is the central hub for monitoring the press and making adjustments in real-time to ensure efficient operation.
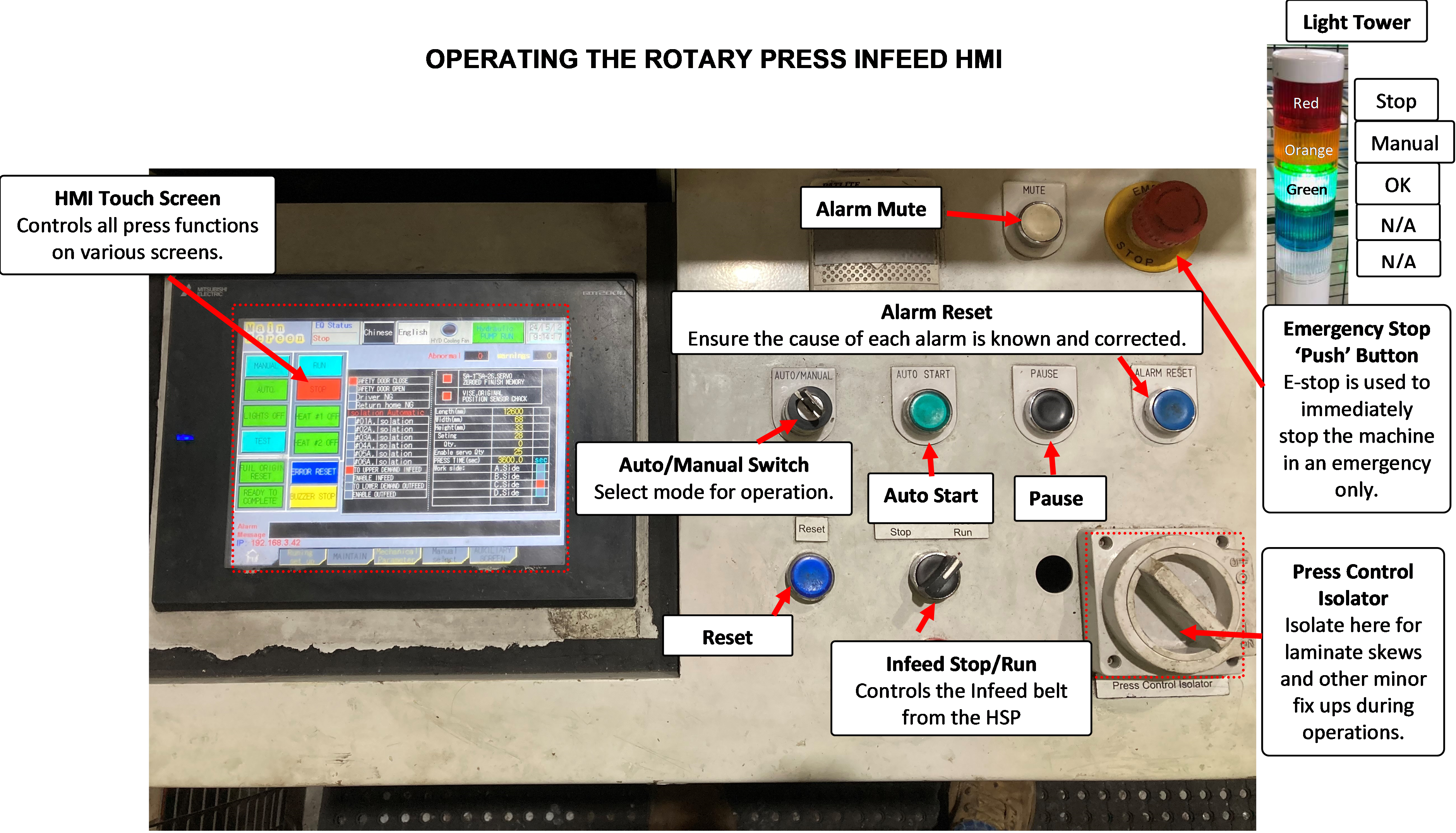
Glue Applicator HMI Overview
Before starting the Rotary Press, it’s essential to complete all necessary pre-operational checks to ensure safe and efficient operation. Follow this checklist to prepare the press for a productive shift. As you complete each task, please tick the corresponding box and sign off on the Pre-Operational Checklist document to confirm that the task has been completed. Any issues encountered during the checks should be reported immediately to your supervisor and/or the maintenance team.
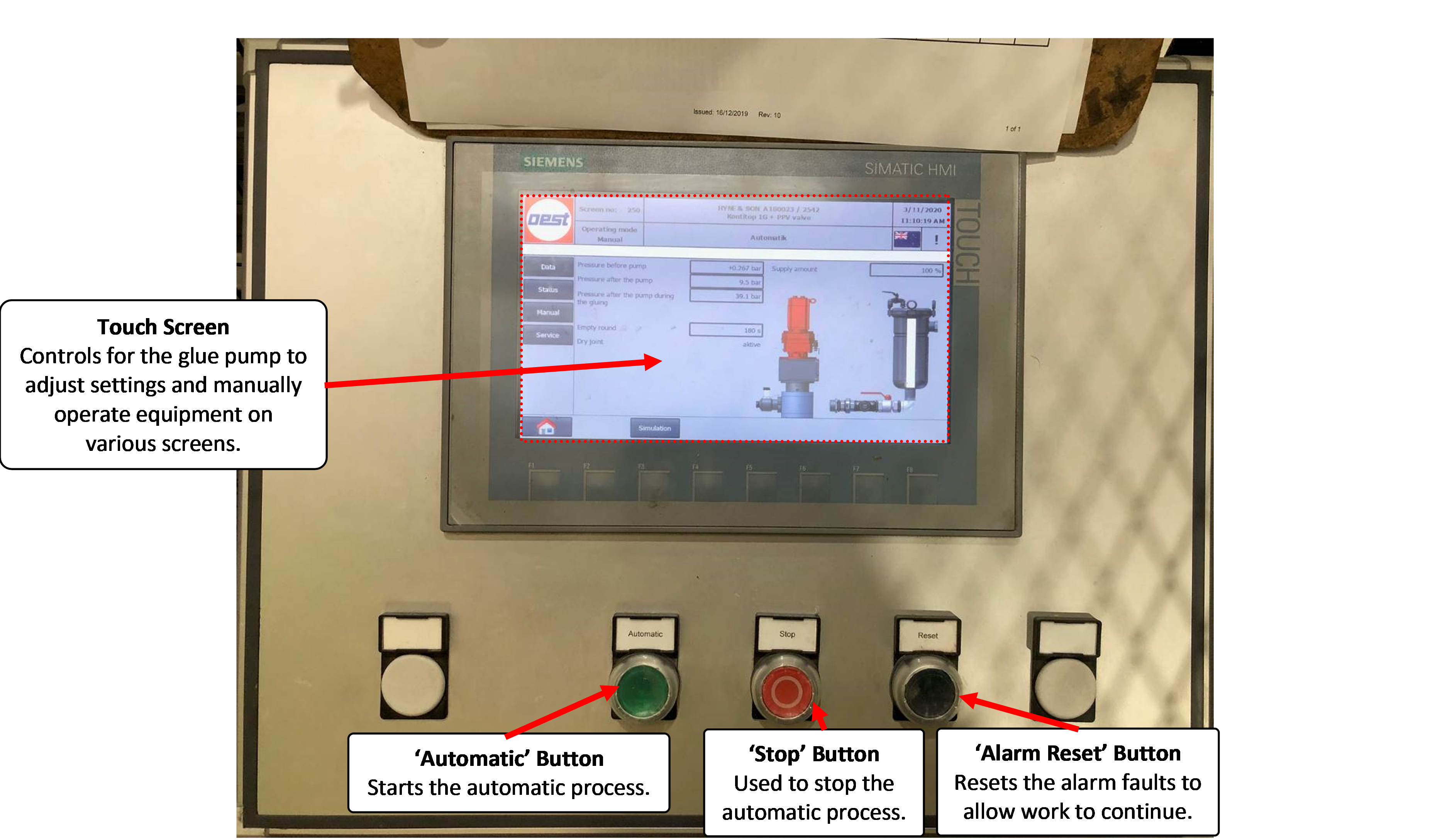
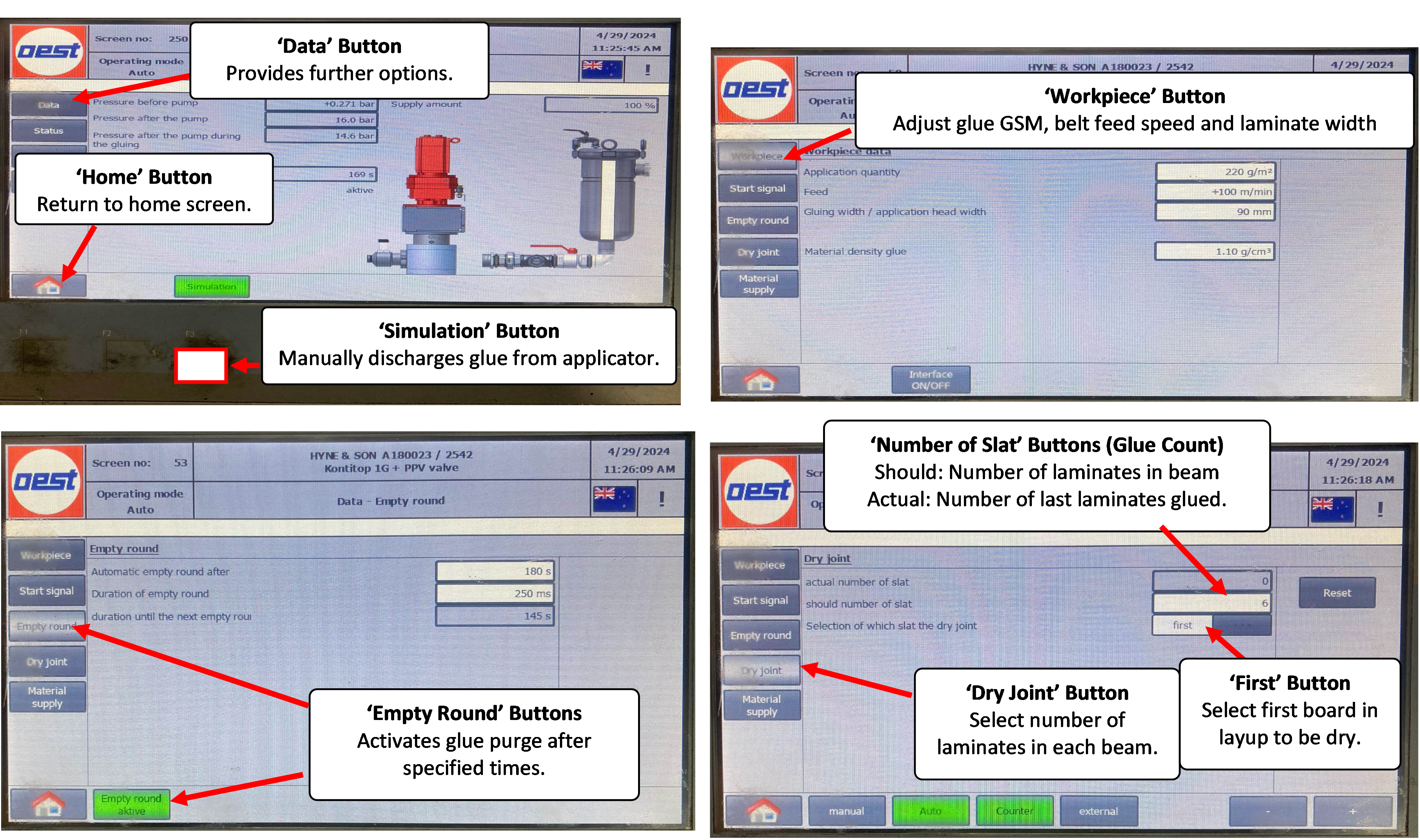
Press Program Sheet Overview
mOperating the rotary press involves tracking important production data using both the Press Program Sheet and the Press Control Sheet. These documents ensure the correct setup, monitoring, and documentation of press runs.
The Press Program Sheet provides all information for the days production run.
- Product – Shows the Grade, Size, & Treatment.
- Job ID # – Shows the Job ID for the Current Press. Must Match the code on Press Production Monitor Screen.
- Recipe – Shows the beam recipe and total number of laminates in each Beam
- Press Times – Record Start Time of Glue Application on the Press Program Sheet for each Beam and End Time once Press has closed.
- Press Details – Record Press Side, Layup Date, Temperature, Humidity, Press Torque, and latest Glue Test GSM
Press Times and Details are also to be recorded in the Daily Press Control Sheet
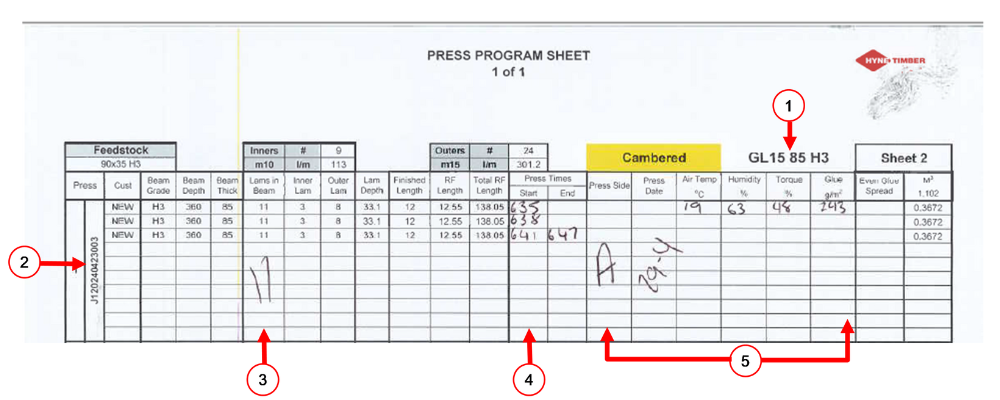
Press Control Sheet Records
- Date – Record Date and Operator’s names.
- Environmental – Record Temperature and Humidity for each Layup.
- Press Times – Record the Start time that glue Is applied to the first board and End time when the press has closed.
- Tension – Record the Tension setting for the press. 35% for 70mm width and 48% for 90mm.
- GSM – Record the latest Glue Spread
- Laminate Size – Used to calculate Cubic Meters pressed daily.
- Cubic Meterage – Using the supplied calculator, record the cubic meters for each press.
- Comments – Record any issues that occur during the press.
- Open Time – The time between when the first laminate is glued and when the press closes.
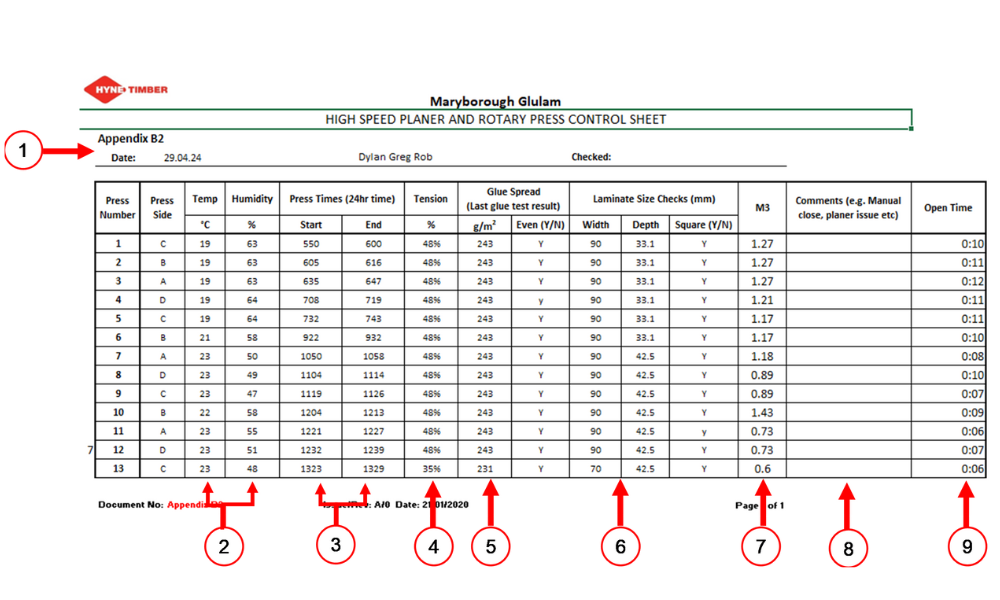
By familiarizing yourself with these key components, you will have a comprehensive understanding of the rotary press system and how to maintain it for optimal performance. In the following modules, you will learn how to safely operate and maintain each component in greater detail.
Preparation/Starting the Press
Several steps must be taken before starting the pressing process to ensure it is completed correctly
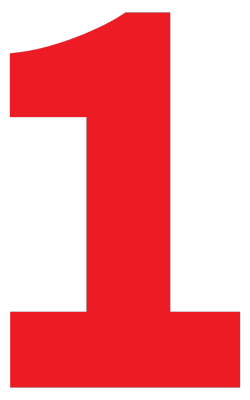
Pull Data for Current Press:
Press “ASKED DATA” to pull the necessary data for the current job.
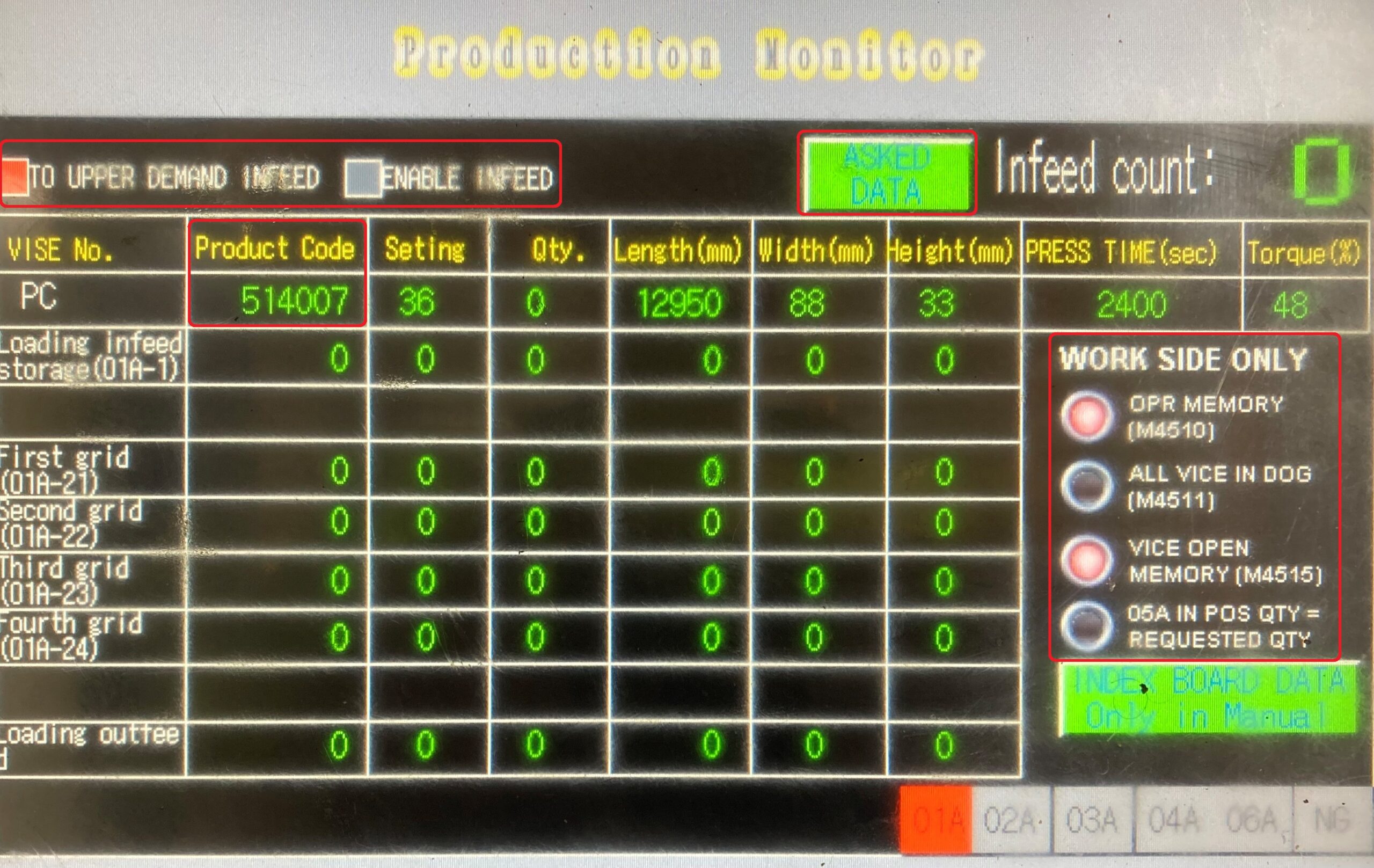
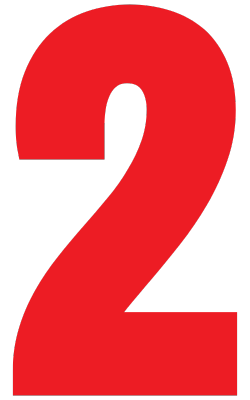
Verify Data Accuracy
Cross-check the displayed data with the job sheet paperwork, including Job ID, quantity, length, and other relevant parameters.
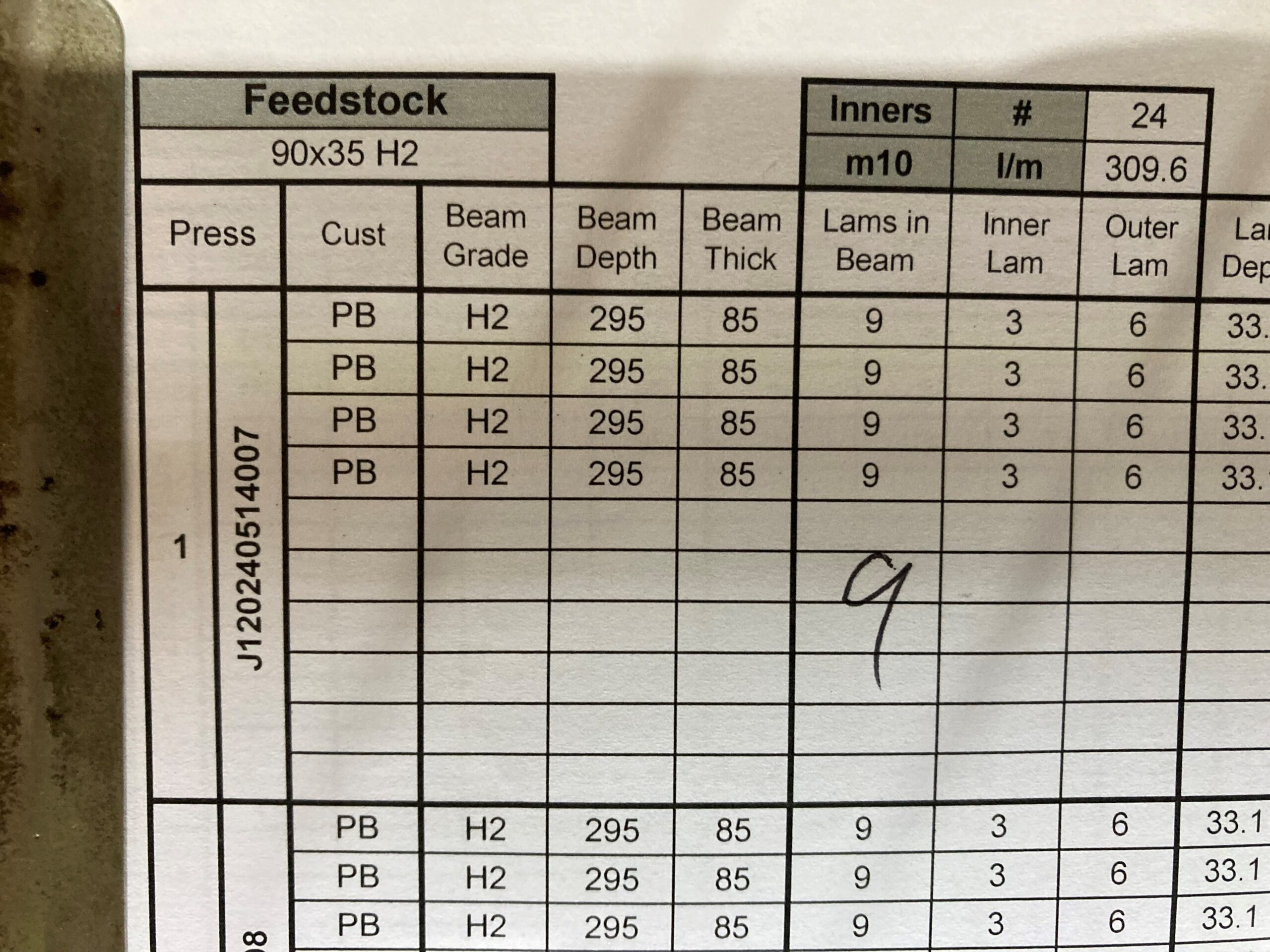
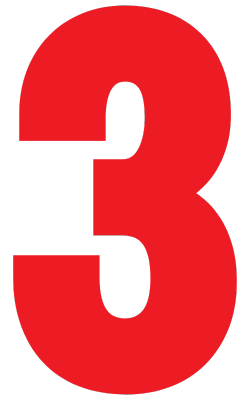
Check Excel Spreadsheet
Ensure that all parameters, including M3 torque, width, depth, and glue rate, are correctly entered in the Excel sheet.
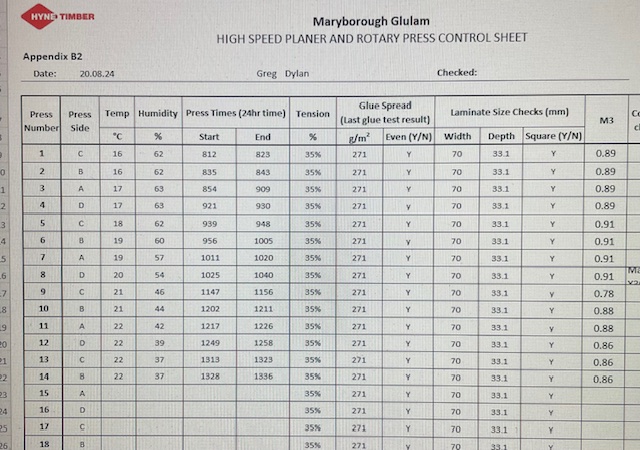
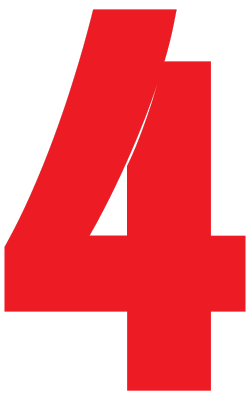
Check Glue Count
Select “Dry Joint” on Glue Applicator HMI and confirm that the number of laminates (lams) per beam matches the paperwork.
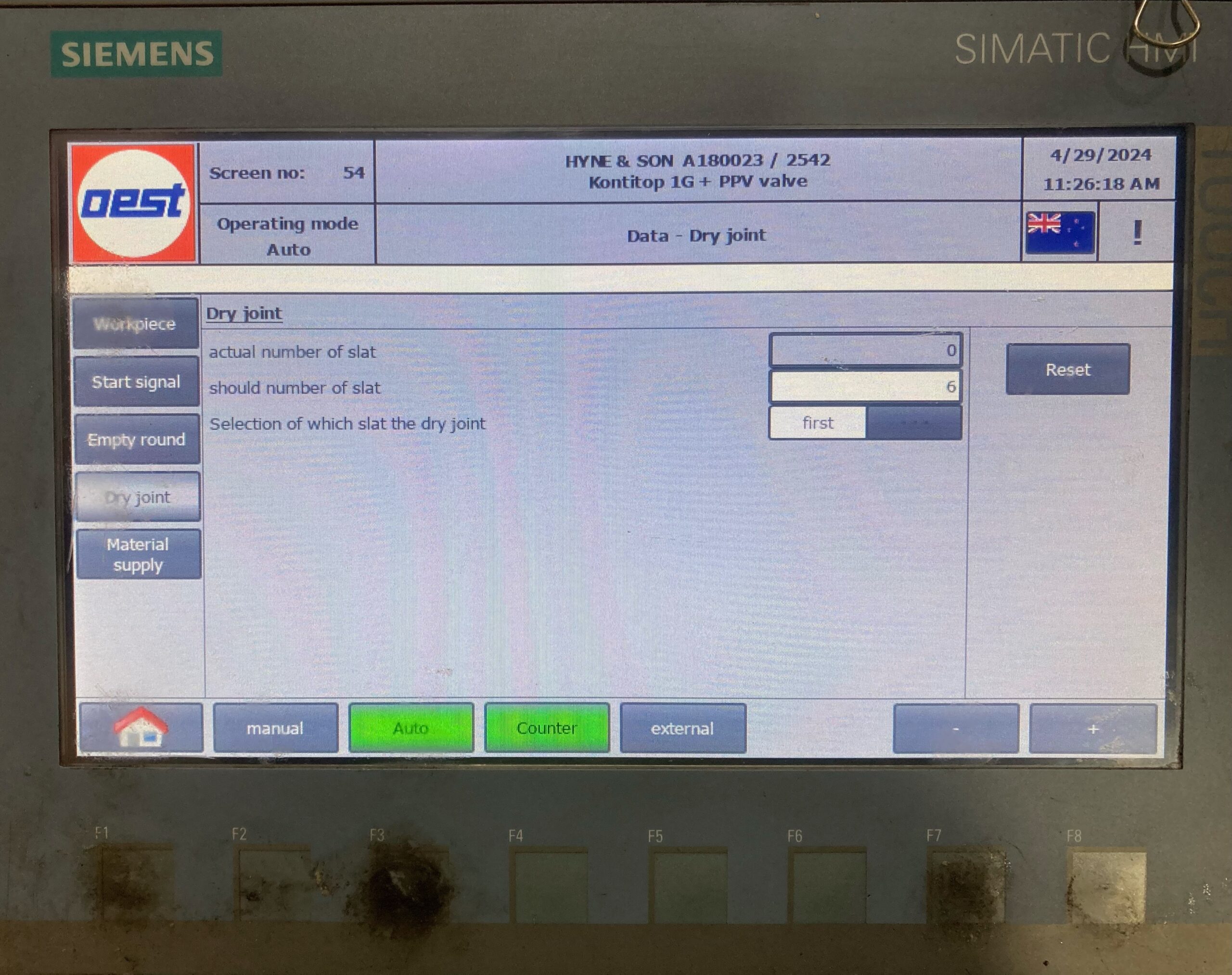
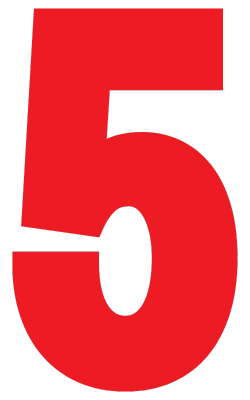
Production Monitor Check
Confirm that the production monitor lights (to upper demand infeed, enable infeed, OPR memory, Vice open memory) are illuminated.
If lights are not illuminated, refer to the troubleshooting guide.
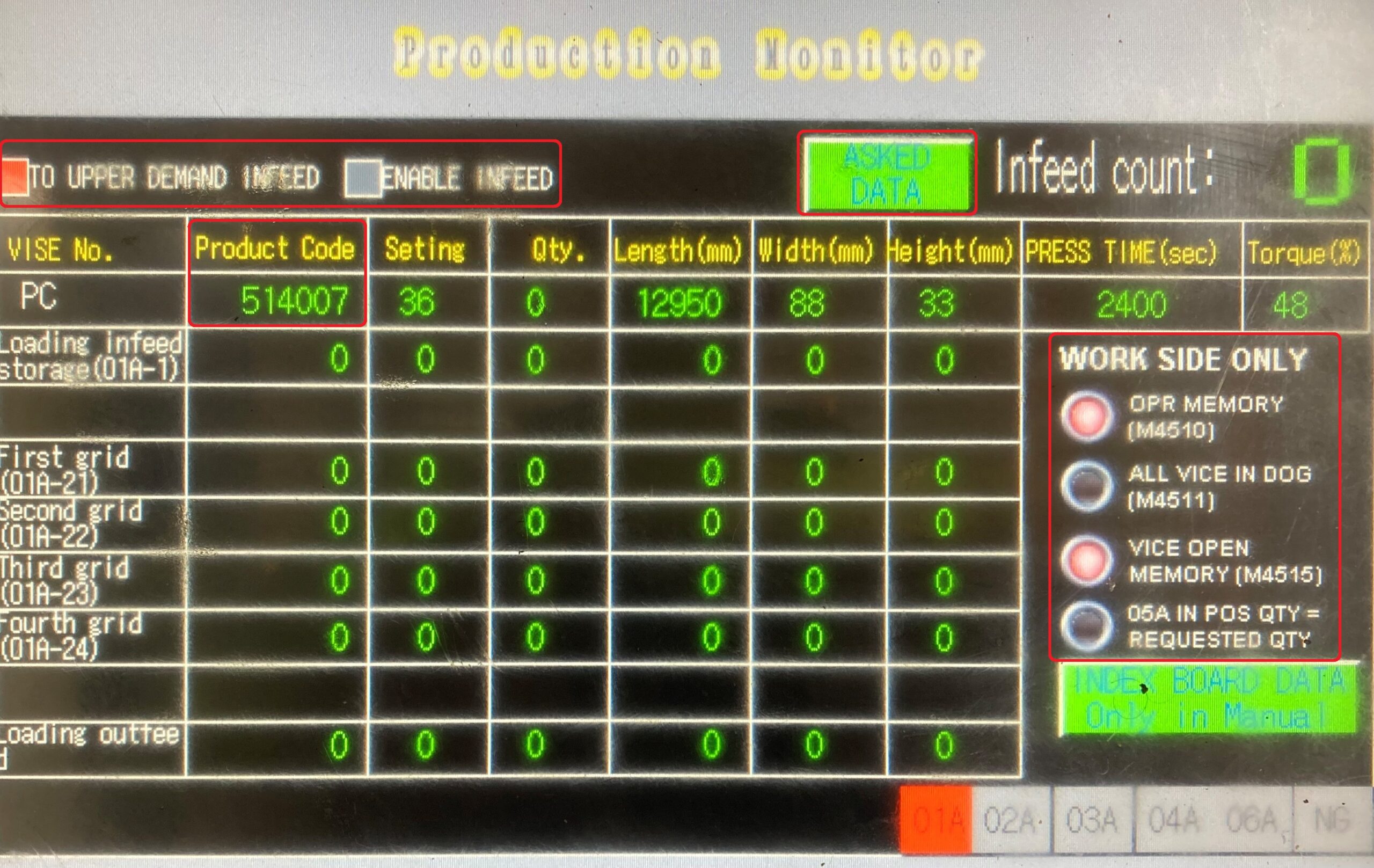
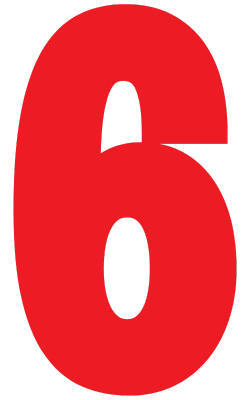
Start the Press
Once all checks are complete and the data is verified, signal the High Speed Planer (HSP) operator to begin running the press.
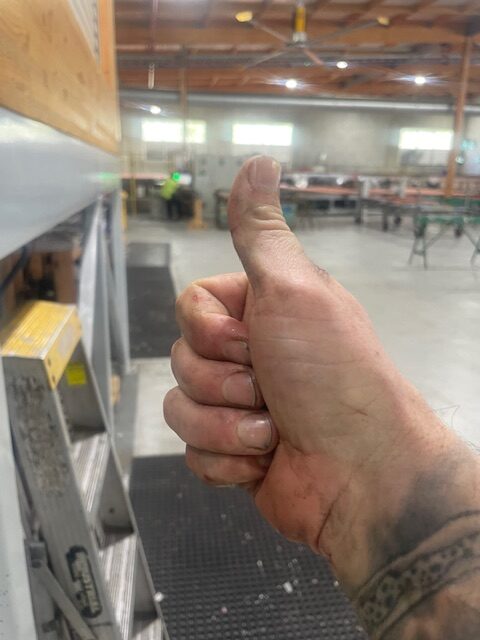
Monitoring Press Operations
Ensuring consistent and safe operation of the rotary press requires continuous monitoring throughout the production process. By keeping a close eye on the machine’s performance, you can quickly identify issues, maintain production quality, and prevent downtime.
Data Recording
Cross-check the displayed data with the job sheet paperwork, including Job ID, quantity, length, and other relevant parameters.
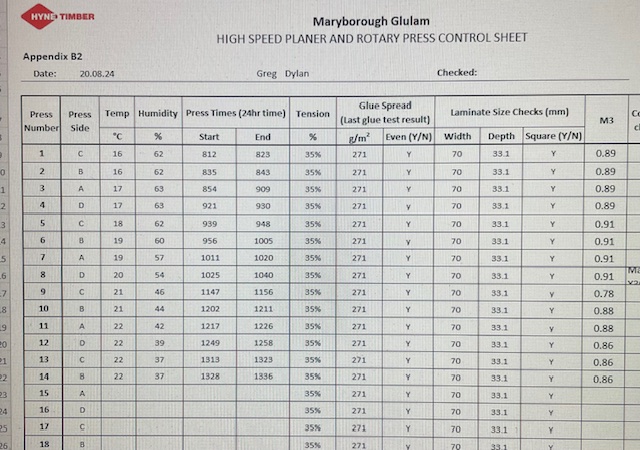
Visual Checks
- Throughout the press operation, monitor each laminate for any damage or defects that could effect the finished product such as broken lams or short lams
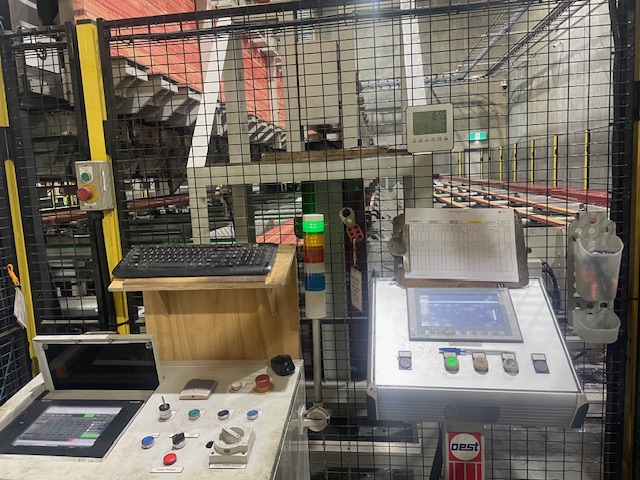
Monitoring Glue Application
- As the press begins its cycle, observe the glue applicator to ensure that it is applying adhesive evenly across the laminates. Inconsistent glue application can lead to weak bonds and product defects.
- If any issues with glue application are noticed, pause the press and make the necessary adjustments to the applicator settings.
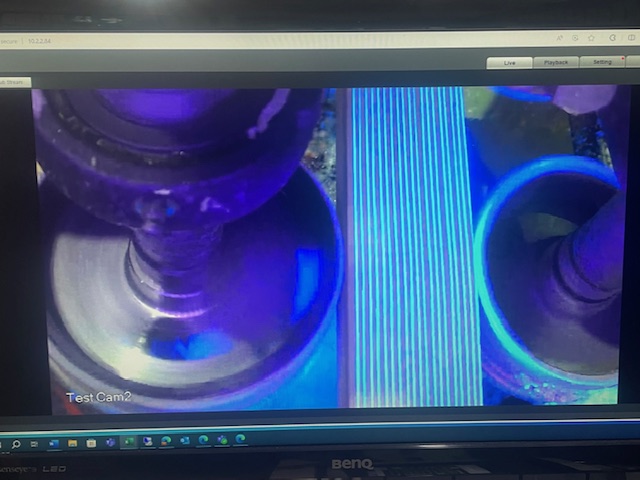
Error and Fault Monitoring
- Continuously monitor the HMI screen for any error codes or alerts. The HMI provides real-time data on the press’s performance, allowing you to quickly identify and address issues.
- Error Codes: The system will display error codes on the HMI when there’s an issue. Monitor these error codes closely, and take immediate action to resolve them based on troubleshooting procedures.
- Sensor Feedback: Ensure that sensors are functioning properly, especially those that detect glue application and laminate positioning. If sensors are malfunctioning, the system may need to be stopped for manual adjustments.
Refer to the troubleshooting module here for detailed information about how to resolve errors or issues that occur during operation of the press
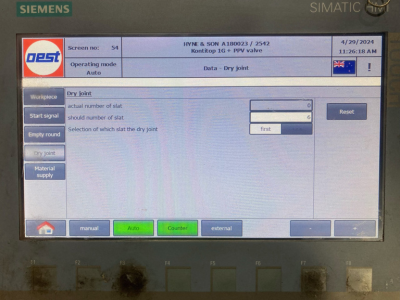
Operator Notes
Throughout the shift, make notes of any anomalies, adjustments, or observations. These notes should be recorded in the Press Control Sheet for future reference and shared with the next operator to ensure smooth transitions between shifts.
Finishing the Press
- Once all laminates required have been run through the infeed, ensure all lams are transferred to the press and vices begin to tighten.
- Once the vices begin to tighten, record press completion time on the spreadsheet
Note: When all lams have been lifted into press and tightened there will be a 2 minute re-torquing time before the press rotates to the next side, the finished beam is dropped out and the process is restarted.