FINGER JOINER TRAINING
Introduction to the Finger Joiner (FJ)
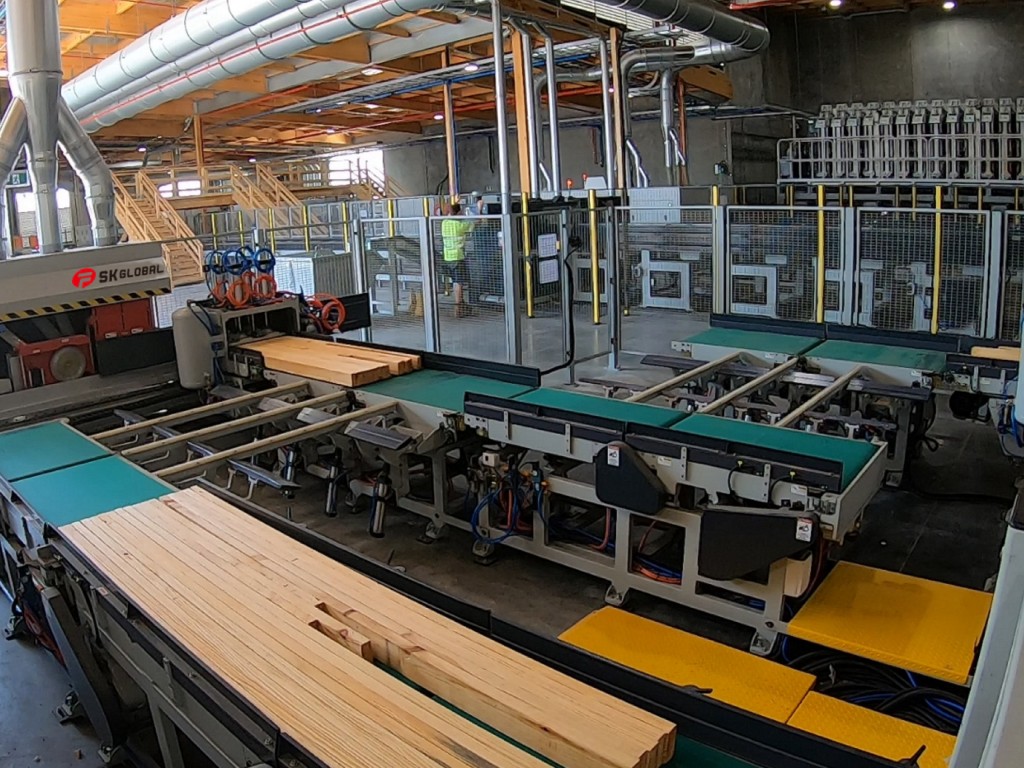
Course Menu
- Back to Main Menu
- Lesson 1 – Introduction
- Lesson 2 – Safety Procedures
- Lesson 3 – Pre-Operational Checks
- Lesson 4 – Operating the Finger Joiner
- Lesson 5 – Operating the Laminate Press
- Lesson 6 – Monitoring the Laminate Deck
- Lesson 7 – Size Changes
- Lesson 8 – Quality Control
- Lesson 9 – When Down,Do
- Lesson 10 – Post-Operational Checks
- Lesson 11 – Competency Quiz
Introduction
The Finger Joiner Workstation is a critical station in the timber production process, responsible for cutting, gluing, joining, and pressing timber laminates into high-quality laminated beams. This workstation combines several machines and automated processes to ensure that each piece of timber meets precise specifications. As an operator, you will be in charge of monitoring the entire process, adjusting machine settings, performing quality checks, and maintaining a safe and efficient work environment.
This module will provide an in-depth introduction to the key components of the Finger Joiner and Laminate Press Workstation, as well as an overview of the primary responsibilities you will have as an operator.
Key Components
To successfully operate the workstation, it is essential to understand the various components that make up the Finger Jointer Workstation:
Finger Joiner (FJ1 & FJ2)
-
Finger Jointer (FJ1 & FJ2)
- The Finger Jointer is where the timber undergoes precise cuts to create finger joints, which are essential for strong, interlocking connections between pieces of timber. The FJ1 cutter performs the initial cut, while FJ2 applies PUR glue to one end of the timber. The cutter heads and trim saws on the FJ are responsible for accurately cutting the timber to size and preparing it for the joining process.
-
PUR Glue Applicator
- The PUR glue applicator is a key component of the Finger Jointer. It applies adhesive to the timber, ensuring that the pieces bond securely during the pressing process. Proper glue application is essential for strong joints and a quality finished product.
-
Auto Flipper
- The Auto Flipper is an automated machine that flips the timber after glue has been applied to one side, allowing the two pieces to be joined. This step ensures that the timber is correctly aligned and bonded before pressing.
-
Laminate Press
- The Laminate Press is where the glued and joined timber pieces are pressed together under high pressure to form a single, solid laminated beam. The press also cuts the timber to the correct length as it is processed.
-
Threading Chains
- The Threading Chains guide the timber through the pressing and cutting process, ensuring that it is aligned and positioned correctly for pressing. These chains are also responsible for moving the timber from the Finger Jointer to the Laminate Press.
-
Laminate Decks
- After the timber has been pressed and cut to length, it is transferred to the Laminate Decks. These decks hold the laminated beams as they dry, ensuring that the timber is stored correctly before further processing or use.
Control Panels & HMI Interface
-
The Control Panels and HMI (Human-Machine Interface) are the central command centers for the High-Speed Planer and Laminate Decks. The operator uses these interfaces to control the process, monitor machine status, and make adjustments as needed.
- HMI Interface: The HMI screen provides real-time data about the machine’s operation. It displays key metrics such as feed speed, laminate sequence, and cutting dimensions. Operators can select recipes, start and stop the automated process, and troubleshoot any issues that arise.
- Automatic and Manual Modes: The system can be run in automatic mode, where the laminates are fed and planed without manual intervention, or in manual mode, where the operator has direct control over each part of the process.
- Jog Feed Switches: These switches allow the operator to manually feed timber forward or backward, useful for precise positioning or troubleshooting.
- Emergency Stops (E-Stops): There are 10 emergency stop buttons located around the workstation for immediate shutdown in the event of a safety issue. Operators should know the location of each E-stop and use them only in emergencies.
The Control Panels give operators access to detailed control over the planer and laminate decks, allowing them to adjust cutter head positions, feed roller pressure, and overall speed to ensure the laminates meet precise specifications.
Key Responsibilities of the Operator
As the operator of the Finger Jointer and Laminate Press Workstation, your role is essential to ensuring a smooth and efficient production process. Below are your key responsibilities:
-
Machine Operation:
- You will be responsible for starting, running, and monitoring the Finger Jointer and Laminate Press machines. This includes setting the correct parameters for timber size, glue application, and pressing pressure, as well as ensuring that the timber is fed through the system correctly.
-
Quality Control:
- As an operator, one of your most critical tasks is performing quality checks throughout the process. This includes monitoring the quality of finger joints, ensuring adequate glue coverage, and inspecting the finished beams for defects such as misaligned joints, stepped finger joints, or insufficient glue squeeze-out.
- You will also need to identify and address common defects, such as knots in the timber, that could affect the structural integrity of the final product.
-
Monitoring the Laminate Deck:
- After pressing, you will be responsible for ensuring that the laminated beams are transferred smoothly to the Laminate Decks for drying. This involves monitoring the alignment of the timber and making sure there are no jams or delays in the transfer process.
-
Pre-Operational and Post-Operational Checks:
- At the start and end of each shift, you will be required to complete pre-operational and post-operational checks to ensure that the workstation is safe, clean, and functioning properly. Pre-operational checks involve inspecting the machine, applying release agents, and making sure all safety measures are in place. Post-operational checks include shutting down the machines, cleaning the glue applicators, and ensuring that the workstation is prepared for the next shift.
-
Handling Size Changes:
- Throughout the production process, there may be times when size changes are required. As an operator, you must be able to adjust the Finger Jointer and Laminate Press to accommodate different timber sizes. This involves isolating the machine, adjusting width and thickness settings, and running test pieces to ensure accuracy.
-
Safety Management:
- Ensuring the safety of yourself and your colleagues is a primary responsibility. This includes wearing the appropriate Personal Protective Equipment (PPE) such as safety glasses, ear protection, gloves, and respirators when working with hazardous chemicals like PUR glue. Additionally, you will need to follow all lockout/tagout and isolation procedures when performing maintenance or size changes.
-
Troubleshooting and Escalation:
- If issues arise during production, such as machine malfunctions or repeated defects in the timber, it will be your responsibility to troubleshoot and resolve the problem. If necessary, escalate more complex issues to your supervisor or the maintenance team to prevent production delays.
Overview of Training Modules
This module is divided into several lessons designed to teach the proper operation, maintenance, and safety procedures for the Finger Jointer and Laminate Press Workstation. Below is an outline of the lessons included in the module:
Lesson 1: Introduction to the Finger Jointer and Laminate Press
- Introduction to the key components of the workstation and an overview of operator responsibilities.
Lesson 2: Required Personal Protective Equipment (PPE)
- Overview of the PPE required for safe operation, including safety glasses, hearing protection, gloves, and respirators when handling hazardous chemicals like PUR glue.
Lesson 3: Pre-Operational Checks
- Step-by-step guide for conducting pre-operational checks, including machine safety checks, area inspections, and the application of release agents.
Lesson 4: Operating the Finger Jointer
- Detailed instructions for operating the Finger Jointer, including how to start Zone B, select product size, and monitor the cutting and gluing process.
Lesson 5: Operating the Laminate Press
- Instructions for operating the Laminate Press, including how to thread the timber through the chains, cut to length, and press laminates.
Lesson 6: Monitoring the Laminate Deck
- How to monitor the laminate deck for proper alignment and transfer of laminated beams for drying.
Lesson 7: Handling Size Changes
- Detailed instructions on how to make size changes to the Finger Jointer and Laminate Press, including adjusting width, thickness, and length settings. This lesson also covers the isolation procedures necessary before making size changes.
Lesson 8: Common Defects and Quality Control
- Instructions for identifying and correcting common defects such as insufficient glue squeeze-out, stepped finger joints, and misaligned timber. This lesson emphasizes quality control measures.
Lesson 9: Post-Operational Checks
- Step-by-step guide for safely shutting down the workstation, cleaning the equipment, and performing maintenance tasks such as cleaning glue applicators and conveyor belts.
By the end of this training, you will have a comprehensive understanding of the Rotary Press and be well-prepared to operate it safely and efficiently, contributing to the overall success of our production process. Let’s get started and make safety and quality our top priorities.