FINGER JOINER TRAINING
Pre-operational Checks
Course Menu
- Back to Main Menu
- Lesson 1 – Introduction
- Lesson 2 – Safety Procedures
- Lesson 3 – Pre-Operational Checks
- Lesson 4 – Operating the Finger Joiner
- Lesson 5 – Operating the Laminate Press
- Lesson 6 – Monitoring the Laminate Deck
- Lesson 7 – Size Changes
- Lesson 8 – Quality Control
- Lesson 9 – When Down,Do
- Lesson 10 – Post-Operational Checks
- Lesson 11 – Competency Quiz
Introduction
Pre-operational checks are essential for ensuring that the HSP workstation is safe and ready for use. These checks help identify potential hazards, ensure that equipment is in working order, and confirm that the workspace is prepared for efficient operation. By performing these checks, operators reduce the risk of equipment failure, workplace accidents, and operational downtime.
This module will guide operators through the detailed steps required to complete pre-operational checks on the HSP workstation, including safety procedures, equipment readiness, and area preparation.
Procedure for Pre-Operational Checks
Pre-operational checks must be performed before starting any shift on the HSP. The first operator on each shift is responsible for completing these checks, recording results, and addressing any issues that may arise. If any equipment or safety concerns are identified, the operator must note the issue, report it, and take appropriate action before the equipment is used.
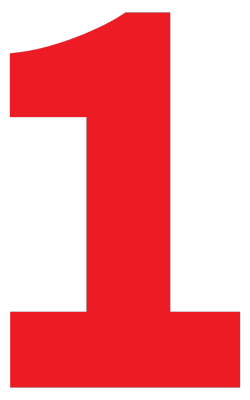
Workspace and Equipment Cleanliness
-
- Was the Area Left Clean from the Previous Shift
- Description:Ensure that the HSP area and surrounding workspace are clean, free of debris, and ready for operation. A tidy workspace is essential for both safety and operational efficiency. Check for any leftover waste, timber scraps, or shavings, and remove them if necessary.
- Action: Clean the area before starting, if required.
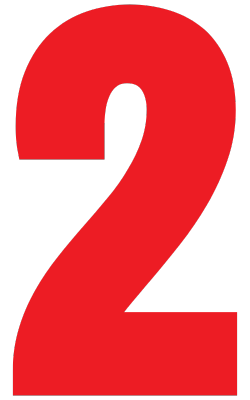
Planer Knife Inspection
- Task: Inspect the Condition of the Knives on Cutter Heads
- Description: Visually inspect the cutter heads’ knives to check for signs of damage or wear. Any dull or damaged knives can affect the quality of the planing process and pose a risk to the machine’s performance.
- Action: If any issues are found, report them immediately to the wood machinist for replacement or repair. Do not proceed with operation until the knives are in good condition.
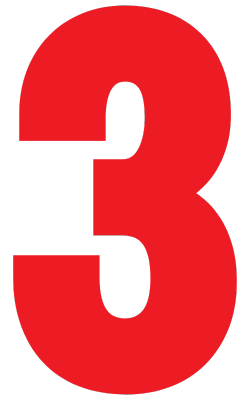
Grease Planer Heads
- Task: Grease the Top & Bottom Heads to 5000 PSI
- Description: Lubricate the top and bottom planer heads using a grease gun to reach the required pressure of 5000 PSI. This ensures the heads are properly lubricated, preventing friction and overheating during operation.
- Action: Apply the necessary amount of grease and verify the pressure level is correct.
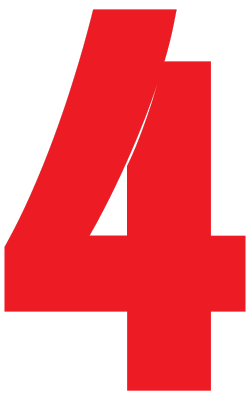
Install Collars & Outriggers
- Description: Install the collars and outriggers to support the HSP for stable and safe operation. These components help balance the machine and ensure smooth functioning.
- Action: Ensure all collars and outriggers are securely installed and properly aligned before starting the HSP.
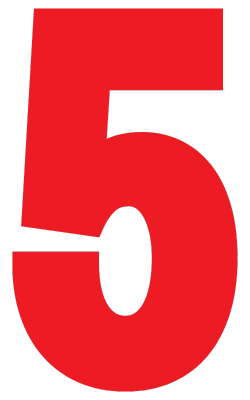
Grease Outriggers
- Task: Grease Outriggers to 4000 PSI
- Description: Lubricate the outriggers by applying grease to a pressure of 4000 PSI. Proper lubrication prevents mechanical stress and allows smooth movements during operation.
- Action: Confirm the correct amount of grease has been applied, and verify that all outriggers are functioning smoothly.
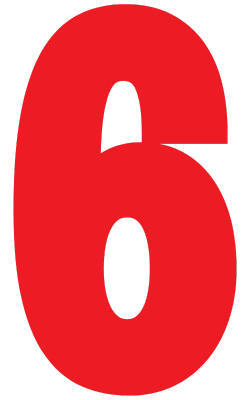
Calibration
- Task: Calibration & Quality Check
- Description: Perform a calibration check to ensure the HSP is correctly set for the upcoming production run. Use calibrated tools such as Vernier calipers to verify the settings for width and thickness.
- Action: Run a test piece to confirm that the machine is producing accurate dimensions and a smooth surface finish. If adjustments are needed, recalibrate the machine before proceeding.
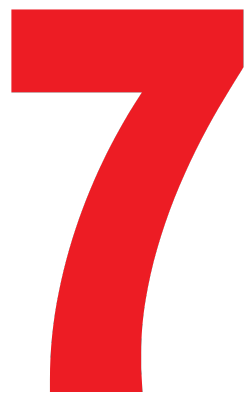
Start up Planer
- Task: Turn On the HSP & Ensure Doors Are Closed
- Description: Power on the High-Speed Planer (HSP) and ensure that all safety doors and guards are properly closed. The machine will not operate unless the doors are securely shut.
- Action: Check that the control panel confirms the machine is ready, and verify that all safety mechanisms are engaged.
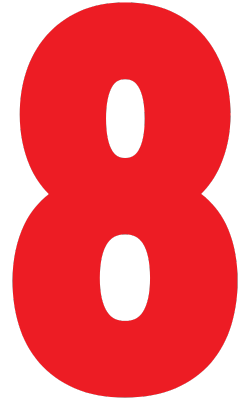
Verify Laminate Count
- Task: Verify the Laminate Count on the Chain Deck
- Description: Confirm that the laminate count on the chain deck matches the job details listed on the board and the HMI system. The correct number of laminates is essential to ensure smooth production and avoid errors during planing.
- Action: Adjust the laminate count if necessary, and ensure the chain deck is ready for operation.
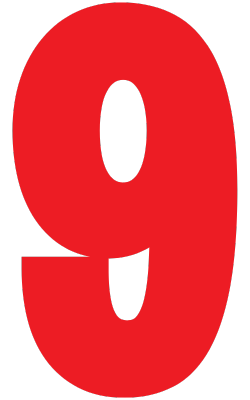
Stirling System Check
- Task: Check & Load Jobs from the Stirling System
- Description: Ensure the correct job data is loaded from the Stirling system. Cross-check the job details with the job sheet to ensure you’re operating under the correct recipe (layup).
- Action: Verify that the HMI displays the correct information and confirm that the job is ready to proceed. If discrepancies are found, reload the job data.
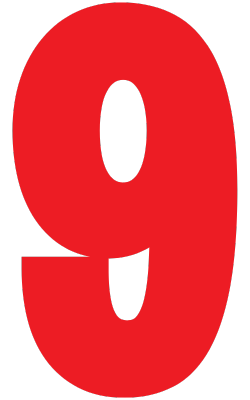
Clear Waste Timber
- Task: Clean up leftover timber
- Description: Clear any leftover timber from the previous shift to ensure the chain deck and surrounding area are free of obstructions. Timber left in the machine could cause jams or production delays.
- Action: Remove all scrap timber, shavings, and waste before starting the production run.
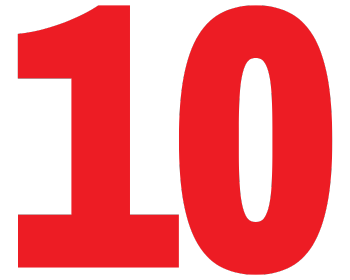
Documentation and Sign-Off
Once all the checks have been completed, document the results on the Pre-Operational Checks Sheet. For each item:
- ✓ if the item meets the standard.
- × if the item does not meet the standard (note the issue and take corrective action).
- NA if the item is not applicable for this shift.
Staff Sign-Off:
-
- Ensure that the first operator of the shift signs off on the checklist, confirming that the pre-operational checks have been completed and any necessary corrective actions have been taken.
Reporting and Taking Action
- If any issues are found during the checks, report them immediately to the maintenance team or supervisor.
- Do not operate the HSP until all issues have been resolved and the machine is safe to use.
End-of-Shift Considerations
Operators are also responsible for ensuring that the HSP section is left clean and ready for the next shift. All tools and materials must be stored properly, and any waste should be disposed of according to plant protocols.
Well Done!
- By following these pre-operational checks, operators ensure that the HSP workstation is safe, efficient, and ready for production. Proper execution of these checks prevents accidents, reduces downtime, and maintains the overall safety and functionality of the equipment.