HIGH SPEED PLANER TRAINING
Introduction to the High Speed Planer (HSP)
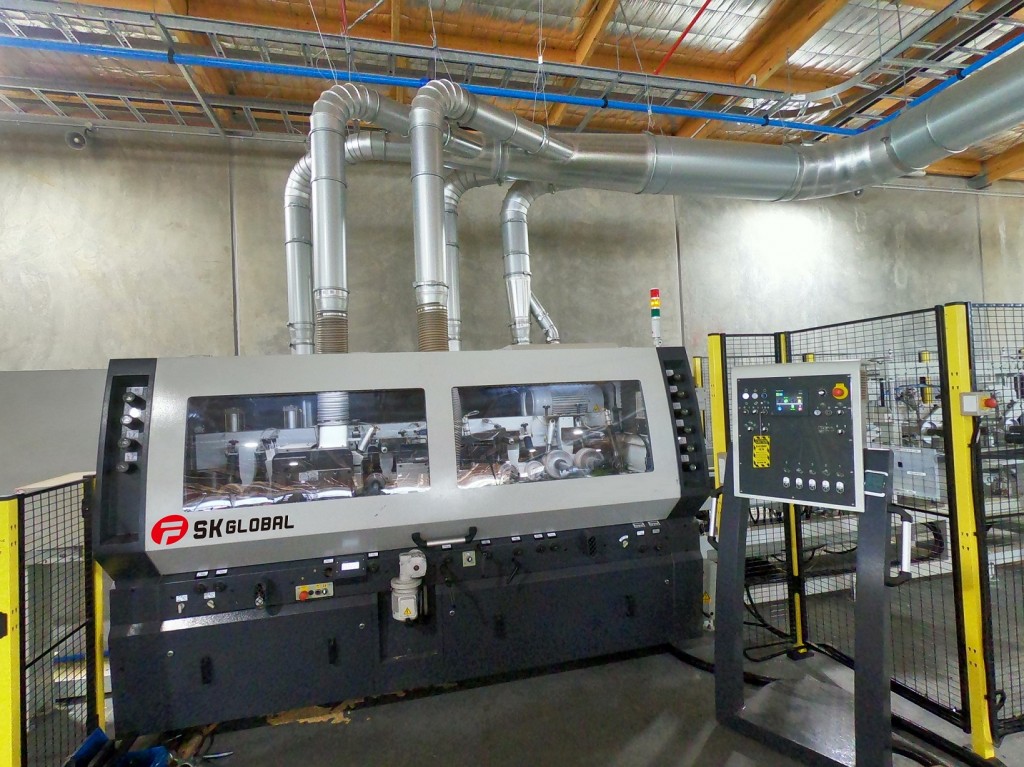
Introduction
The High-Speed Planer (HSP) is a critical area in the production process, designed to efficiently prepare and dress timber laminates for gluing and pressing into laminated beams. The purpose of this module is to provide operators with a comprehensive understanding of how to safely and effectively operate the HSP and Laminate Decks, ensuring high-quality output while maintaining safety standards.
Key Components
Understanding the key components of the High-Speed Planer and Laminate Decks is crucial for safe and efficient operation. Below is an overview of these components and their functions:
High-Speed Planer
The High-Speed Planer is a sophisticated machine designed to dress laminates by trimming and shaping them on all four sides, ensuring uniform thickness and smooth surfaces. It operates at high speeds (up to 80 meters per minute), using multiple cutter heads to precisely shape the laminates before they move on to the glue applicator and press.
- Cutter Heads: The HSP uses five cutter heads positioned on the top, bottom, and sides of the timber. These cutter heads can be adjusted to meet the required width and thickness of the laminate.
- Feed Rollers: These rollers guide the timber laminates through the planer. They apply consistent pressure to ensure that the timber feeds evenly through the cutting area.
- Planer Bed and Sound/Safety Hood: The planer bed supports the laminates during the trimming process, while the sound/safety hood reduces noise levels and protects operators from flying debris. The hood must be closed during operation.
- Bed Lubricant System: This system ensures that the planer bed remains lubricated, preventing jams and damage to the timber during the feeding process.
- Dust Extraction System: The planer is equipped with a dust extraction system to remove shavings and maintain a clean working environment, essential for the longevity of the machine and the quality of the product.
Laminate Decks
The Laminate Decks play a critical role in the feeding process. They are responsible for automatically sorting and delivering inner and outer laminates to the High-Speed Planer. The decks operate via a series of conveyors and chains that organize the laminates in the correct sequence according to the day’s production recipe.
The laminate decks consist of the outfeed chains (15A) from the finger jointer press, lift switch (diverter) chains (16A), 2 chain decks (17A) for outer laminates (lower chain – deck A) and inner laminates (upper chain – deck B), lift switch chains (18A), drop out gates (19A).
- Deck A (Outer Laminates): This lower deck handles the outer laminates that form the top and bottom layers of the laminated beams. Outer laminates typically have higher-grade specifications (e.g., M15).
- Deck B (Inner Laminates): The upper deck handles inner laminates, which make up the interior layers of the beam. These laminates are of a slightly lower grade (e.g., M10 or M12) but still need to meet quality standards.
- Drop-Out Gates: These gates allow operators to remove defective laminates from the production line and replace them with new ones, ensuring consistent quality.
- Lift Switch Conveyors: These conveyors transport the laminates between the sorting decks and the planer, making sure they are delivered in the correct order for each beam’s layup.
The laminate decks minimize manual handling, which improves efficiency and reduces the risk of injury. However, the operator must still monitor the process closely to ensure smooth operation and address any jams or misalignments.
Control Panels & HMI Interface
-
The Control Panels and HMI (Human-Machine Interface) are the central command centers for the High-Speed Planer and Laminate Decks. The operator uses these interfaces to control the process, monitor machine status, and make adjustments as needed.
- HMI Interface: The HMI screen provides real-time data about the machine’s operation. It displays key metrics such as feed speed, laminate sequence, and cutting dimensions. Operators can select recipes, start and stop the automated process, and troubleshoot any issues that arise.
- Automatic and Manual Modes: The system can be run in automatic mode, where the laminates are fed and planed without manual intervention, or in manual mode, where the operator has direct control over each part of the process.
- Jog Feed Switches: These switches allow the operator to manually feed timber forward or backward, useful for precise positioning or troubleshooting.
- Emergency Stops (E-Stops): There are 10 emergency stop buttons located around the workstation for immediate shutdown in the event of a safety issue. Operators should know the location of each E-stop and use them only in emergencies.
The Control Panels give operators access to detailed control over the planer and laminate decks, allowing them to adjust cutter head positions, feed roller pressure, and overall speed to ensure the laminates meet precise specifications.
Key Responsibilities of the Operator
The operator plays a crucial role in ensuring the smooth and safe functioning of the HSP and Laminate Decks workstation. Below are the primary responsibilities:
Pre-Operational Checks:
-
- Perform thorough pre-operational checks to ensure that all equipment is functioning properly and safely. This includes inspecting safety guarding, checking for air or oil leaks, ensuring E-stops are operational, and verifying that the planer and glue applicator are properly set up.
- Complete all required pre-start checklists and log any maintenance needs.
Machine Operation:
-
-
- Laminate Decks: Manage the laminate decks by selecting the correct laminates for each beam layup, monitoring the conveyor system, and addressing any jams or misfeeds.
- High-Speed Planer: Operate the planer by setting the correct speed, adjusting the feed rollers, and ensuring that the timber is dressed to the correct dimensions. The operator must also monitor the cutting heads and ensure that the surfaces are smooth and ready for gluing.
- Glue Applicator: Monitor the glue flow rate and ensure a consistent application of glue to the laminates before they proceed to the pressing stage.
-
Process Monitoring:
-
- Continuously monitor the automated process via the HMI control panel. This includes keeping track of key performance indicators such as timber feed speed, laminate quality, and the layup sequence.
- Troubleshoot any issues that arise during operation, such as jams, misaligned laminates, or incorrect layup sequences. The operator should intervene promptly to prevent production delays.
Quality Control:
-
- Ensure that all laminates meet the quality specifications for the product being manufactured. This involves checking for defects such as insufficient glue squeeze-out, tip gaps, or stepped finger joints.
- Defective laminates must be identified and removed from the production line using the drop-out gates.
Troubleshooting and Downtime Recording:
-
- If the machinery malfunctions or if any part of the process is not operating as expected, the operator must troubleshoot the issue using the HMI interface or manual controls.
- Accurately record any downtime and categorize the issue. This information is critical for production targets and maintenance scheduling.
Overview of Training Modules
This training program is designed to equip you with the knowledge and skills necessary to operate the High-Speed Planer (HSP) safely and effectively. The modules are structured as follows:
Lesson 2 – Safety Procedures
Learn critical safety protocols specific to the High-Speed Planer, including proper use of Personal Protective Equipment (PPE), handling of emergency stop (E-Stop) buttons, and safe operation of isolation procedures to ensure a hazard-free work environment.
Lesson 3 – Pre-Operational Checks
Understand how to conduct thorough pre-operational checks, including inspecting cutter heads, checking lubrication levels, and ensuring that the safety mechanisms are in place before starting the High-Speed Planer. This lesson will also cover ensuring that the surrounding work area is prepared and clear of hazards.
Lesson 4 – Operating the High-Speed Planer
A detailed guide on how to start, operate, and monitor the High-Speed Planer for optimal performance. This module covers the step-by-step process of planing timber laminates, monitoring pressure and speed settings, and ensuring that the laminates are processed according to specifications.
Lesson 5 – Laminate Deck Operation
Learn how to monitor and operate the Laminate Deck, ensuring proper alignment and spacing of laminated beams as they dry. This module will focus on ensuring uniform drying, managing beam transfers, and troubleshooting common issues like jams or misaligned laminates.
Lesson 6 – Size Changes
Discover the proper procedures for adjusting the High-Speed Planer for different timber sizes. This lesson covers adjusting width and thickness settings on the planer, press, and laminate deck, as well as how to conduct test runs to confirm the accuracy of size changes.
Lesson 7 – Troubleshooting
Identify and resolve common issues that arise during operation, including uneven cuts, glue application problems, or misaligned laminates. This module will also cover handling error codes on the Human-Machine Interface (HMI) and manual operation procedures when needed.
Lesson 8 – Downtime Procedures
Learn the routine tasks that should be completed during downtime. This includes cleaning the cutter heads and belts, performing general maintenance, checking for wear and tear, and preparing the HSP for the next production cycle.
Lesson 9 – End-of-Shift Procedures
This lesson focuses on the proper shutdown of the High-Speed Planer. Learn how to safely power down the machine, clean the components, inspect the planer for any issues, and ensure the workstation is organized and ready for the next shift.
Lesson 10 – Competency Quiz
Test your knowledge with a competency quiz that verifies your understanding of the key processes and safety protocols for operating the High-Speed Planer. This final assessment will ensure you are fully prepared to handle the HSP independently and contribute effectively to the production process.
By the end of this training, you will have a comprehensive understanding of the High-Speed Planer and Laminate Deck operations. You will be well-prepared to operate the machinery safely and efficiently, ensuring that quality and productivity are maintained. Let’s begin, keeping safety and excellence at the forefront of everything we do!