FINGER JOINER TRAINING
When Down, Do: Checklist
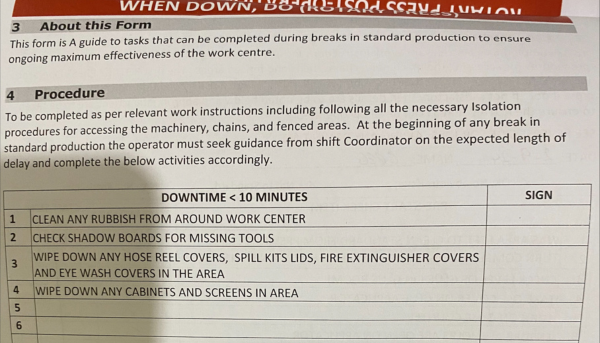
Course Menu
- Back to Main Menu
- Lesson 1 – Introduction
- Lesson 2 – Safety Procedures
- Lesson 3 – Pre-Operational Checks
- Lesson 4 – Operating the Finger Joiner
- Lesson 5 – Operating the Laminate Press
- Lesson 6 – Monitoring the Laminate Deck
- Lesson 7 – Size Changes
- Lesson 8 – Quality Control
- Lesson 9 – When Down,Do
- Lesson 10 – Post-Operational Checks
- Lesson 11 – Competency Quiz
Introduction
During breaks in production or periods of downtime, it’s important to utilize the time effectively to maintain your workstation and ensure readiness for the next run. Depending on the length of the downtime, complete the tasks listed below. Be sure to tick off each task as itโs completed.
DOWNTIME LESS THAN 10 MINUTES
For short breaks in production (under 10 minutes), operators should focus on small tasks that can be completed quickly without interfering with machine operations:
-
Cut Up Broken or Non-Conforming Laminates
- Remove any damaged or non-conforming laminates from the floor and process them for disposal or recycling.
-
Remove Non-Conforming Boards from Chain Deck
- Inspect the chain deck and remove any non-conforming boards that should not proceed through the production line.
-
Re-Run Boards to Infeed
- Send non-conforming or incorrectly processed boards back to the infeed to be re-run through the planer.
-
Clean Table Area
- Remove rubbish, old paperwork, and debris from the table area to maintain a tidy workspace.
-
Wipe Down Hose Reels, Covers, Spill Kits, and Fire Extinguisher Covers
- Clean and inspect hose reels, safety equipment, and covers to ensure they are in good working order.
-
Wipe Down Cabinets and Screens
- Clean cabinets, screens, and other surfaces in the area to maintain cleanliness and organization.
Clean Any Rubbish from Around Workstation
- Task: Pick up and dispose of any rubbish in your immediate work area.
- Description: Ensure that the workstation is free from clutter and waste, promoting a clean and safe environment.
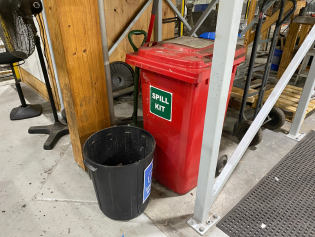
Check Shadow Boards for Missing Tools
- Task: Inspect the shadow boards to ensure all tools are accounted for.
- Description: Make sure that all tools are in their designated spots on the shadow boards. Report any missing tools immediately.
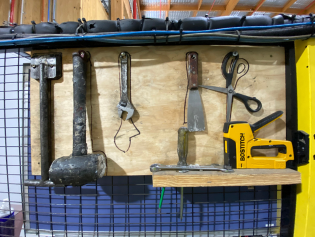
Wipe Down Equipment Covers
- Task: Clean the covers of essential safety equipment.
- Description: Use a cloth to wipe down the hose reel covers, spill kit lids, fire extinguisher covers, and eye wash covers to keep them clean and accessible.
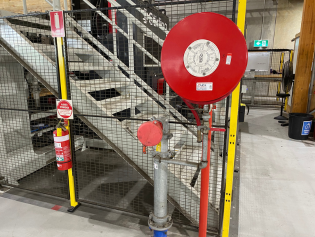
Wipe Down Cabinets and Screens
- Task: Clean any cabinets and screens within your workstation area.
- Description: Wipe down cabinets and screens to remove dust, fingerprints, and debris, ensuring a clean work environment.
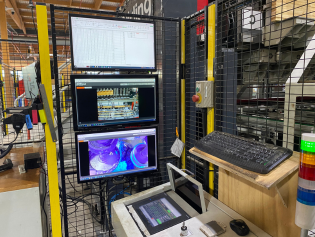
DOWNTIME 10-20 MINUTES
For slightly longer breaks in production (10-20 minutes), operators can complete more extensive cleaning and organizational tasks:
-
Sweep Down Dance Floor Area
- Sweep the main working area (often referred to as the “dance floor”) to remove dust, debris, and waste materials.
-
Empty Rubbish Bins
- Check and empty any rubbish bins located in the working area to prevent overflow.
- Wipe Down Staircase Rails
- Clean the staircase rails to remove dust and maintain cleanliness for staff using the stairs.
Empty Rubbish Bins
-
- Task: Empty all rubbish bins in your workstation area.
- Description: Dispose of the waste from rubbish bins and replace the liners to ensure bins are ready for use.
- Picture Suggestion: Display the process of emptying rubbish bins.
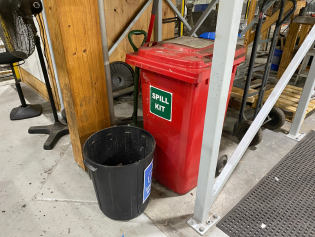
Clean Timber from "Dance Floor"
- Task: Remove any timber debris from the Dance Floor area.
- Description: Ensure that the Dance Floor is clear of timber pieces and other debris, making it safe and ready for the next use.
- Picture Suggestion: Show the Dance Floor being cleaned of timber debris.
Tidy Glue Bench
- Task: Organize and clean the glue bench.
- Description: Straighten up the glue bench, putting away tools and materials, and clean any glue spills to keep the area tidy.
- Picture Suggestion: Display a clean and organized glue bench.
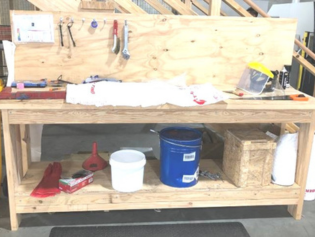
DOWNTIME MORE THAN 20 MINUTES
For longer breaks in production (more than 20 minutes), more involved cleaning and maintenance tasks should be performed:
- Vacuum Out Back of HSP
- Use a vacuum to clean out the back of the HSP, removing dust and debris that may have accumulated.
- Clean Inside HSP Area of Boards and Dust
- Thoroughly clean the interior of the HSP, removing any loose boards and dust to ensure the machine is ready for the next production cycle.
- Clean Glue Bench Area
- Clean the glue bench area, removing any glue residue or waste materials to maintain a clean working environment.
- Clean Up Broken or Loose Boards Around the HSP and FJ Press Area
- Inspect the area around the HSP and finger jointer (FJ) press for any broken or loose boards. Clear away these materials to keep the area organized and safe.
Blow Out Inside of Press Area
-
- Task: Use compressed air to blow out excess glue and knots from inside the press area.
- Description: Clear out any buildup of glue and wood knots within the press to maintain smooth operation.
- Picture Suggestion: Show the press area being cleaned with compressed air.
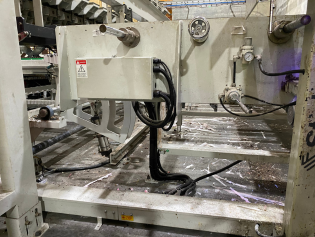
Clean Excess Glue Off Press Lifters
- Task: Scrape and clean off any excess glue from the press lifters.
- Description: Ensure that the press lifters are free of dried glue to prevent operational issues.
Clean Glue Room
- Task: Thoroughly clean the glue room, including all surfaces and equipment.
- Description: Wipe down surfaces, remove any glue spills, and ensure the room is clean and organized for the next production run.
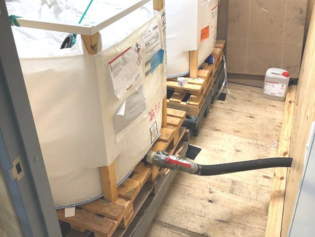
Replace Plastics on Glue Bench if Required
- Task: Replace any worn or damaged plastic coverings on the glue bench.
- Description: Inspect the plastic coverings on the glue bench and replace them as needed to maintain a clean and functional workspace.
Procedure During Downtime
Isolate Equipment:
- Before beginning any downtime activities, ensure that all relevant isolation procedures have been followed to safely access the machinery and surrounding areas.
Seek Guidance:
- At the start of any downtime, consult with the Shift Coordinator to determine the expected length of the delay. This will guide you in selecting the appropriate tasks to complete during the downtime.
Well Done!
- Use this checklist to ensure that all tasks are completed effectively during downtime. Remember to tick off each task as you finish it and report any issues to your supervisor or maintenance team. You can access and complete the When Down, Do Checklist here