FINGER JOINER TRAIING
Monitoring the Laminate Deck
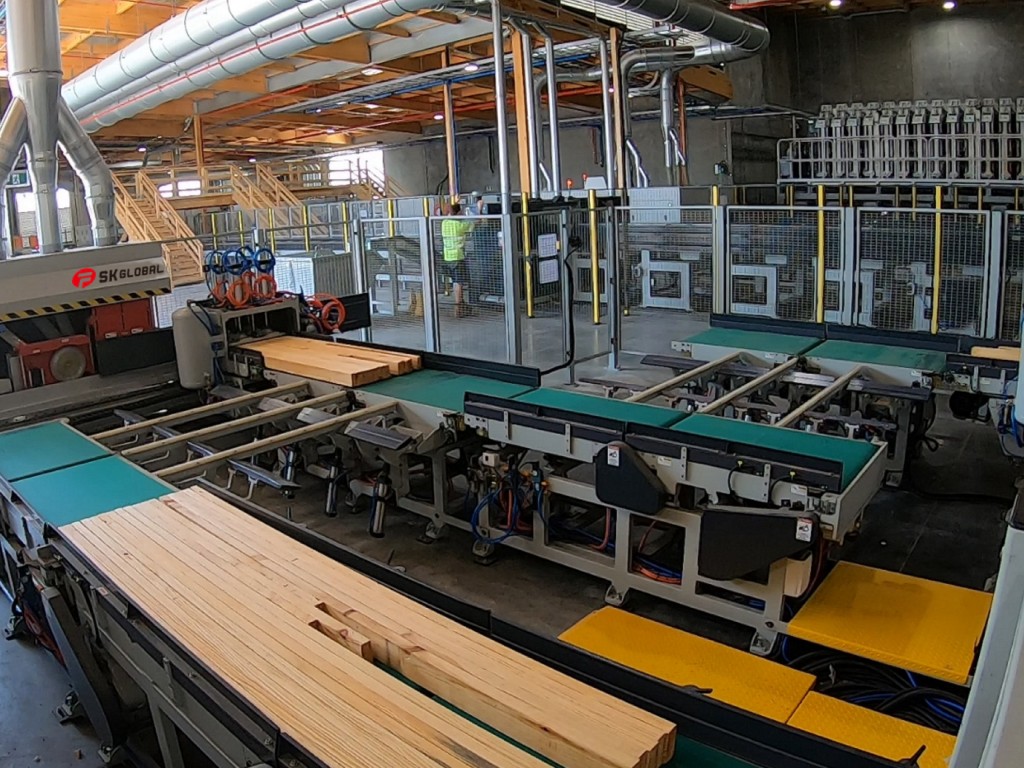
Course Menu
- Back to Main Menu
- Lesson 1 – Introduction
- Lesson 2 – Safety Procedures
- Lesson 3 – Pre-Operational Checks
- Lesson 4 – Operating the Finger Joiner
- Lesson 5 – Operating the Laminate Press
- Lesson 6 – Monitoring the Laminate Deck
- Lesson 7 – Size Changes
- Lesson 8 – Quality Control
- Lesson 9 – When Down,Do
- Lesson 10 – Post-Operational Checks
- Lesson 11 – Competency Quiz
Introduction
Overview
The Laminate Deck is the final stage in the production process at the Finger Jointer Workstation. Once the laminated beams have been pressed, they are transferred to the Laminate Deck for drying. Proper monitoring and operation of the Laminate Deck is essential to ensure that the beams dry uniformly, maintain their quality, and are stored correctly for further processing. This module will teach you how to effectively monitor and operate the Laminate Deck, as well as how to handle common issues that may arise during this stage of production.
By the end of this module, you will be able to:
- Safely transfer laminated beams to the Laminate Deck.
- Monitor the alignment and placement of beams on the deck.
- Identify and resolve common issues related to drying and storage.
Step-by-Step Process for Monitoring and Operating the Laminate Deck
Step 1: Transferring Laminates to the Deck
After the laminated beams are pressed in the Laminate Press, they are moved to the Laminate Deck for drying. Proper placement is crucial for uniform drying and maintaining the quality of the beams.
-
Ensure Correct Alignment:
- As the laminates exit the press, check that they are aligned correctly on the threading chains and conveyors. Misaligned laminates can cause issues in the drying process and may lead to structural defects.
-
Transfer Beams Using the Deck Controls:
- Use the Human-Machine Interface (HMI) to control the transfer of laminates from the press to the Laminate Deck. Ensure the automated system is running smoothly and that the transfer occurs without jams or misalignment.
-
Monitor for Obstructions:
- Regularly check the decking area for any potential obstructions that may interfere with the laminates’ movement. Stop the process and clear the obstruction immediately if needed.
Step 2: Ensuring Proper Spacing and Air Circulation
For the laminates to dry uniformly and maintain structural integrity, proper spacing and air circulation on the deck are essential.
-
Maintain Adequate Spacing:
- Ensure that the laminates are spaced correctly on the deck. Too little space between the beams can cause uneven drying, leading to defects such as warping or cracking.
-
Check Airflow:
- Verify that airflow is unobstructed around all laminates. The drying process relies on adequate air circulation to remove moisture evenly. If airflow is insufficient, adjust the placement of the laminates or increase the spacing between them.
Step 3: Operating the Laminate Deck Controls
The Laminate Deck may include automated controls for managing beam transfers and storage. Understanding how to operate these controls is important for ensuring smooth operations.
- Using the Control Panel:
- The control panel allows you to manage beam transfers, stop and start the deck, and monitor the drying process. Familiarize yourself with the deck’s control system and how to use it efficiently.
- Monitoring Deck Status:
- Keep an eye on the control panel to track the status of the deck and the progress of the beams through the drying process. Any alerts or issues will be displayed on the panel, and you must address them promptly to avoid delays.
Step 4: Monitoring for Quality Issues
Continuous monitoring of the laminates is necessary to catch potential issues early and ensure product quality.
- Inspect for Defects:
- As the laminates dry, inspect them for any defects such as warping, cracking, or uneven glue coverage. Address any issues immediately by adjusting the deck settings or reprocessing defective laminates.
Step 5: Tracking and Counting Laminates
Step 6: Monitoring for Safety
Operating the Laminate Deck requires attention to safety protocols, as beams are heavy and machinery is involved in their transfer and handling.
-
Wear Appropriate PPE:
- Always wear safety glasses, gloves, and steel-toed boots when working near the Laminate Deck, especially during beam transfers and inspections.
-
Monitor for Hazards:
- Be aware of any potential trip hazards or obstructions in the Laminate Deck area. Keep the workspace clear to avoid accidents, especially during beam transfers.
-
Follow Lockout/Tagout Procedures:
- If any maintenance is required on the Laminate Deck or its control systems, follow the proper lockout/tagout procedures to ensure the equipment is de-energized before performing any repairs.
Conclusion
The Laminate Deck plays a critical role in the drying and final preparation of laminated beams. By following the steps in this module, you will ensure that the beams are transferred, spaced, and dried properly, maintaining high-quality standards throughout the process. Remember to monitor the deck continuously, address any issues promptly, and follow safety protocols to ensure smooth operations.
In the next lessons, you will learn more about quality control checks and performing post-operational checks at the Finger Jointer Workstation.
Key Components
Understanding the key components of the High-Speed Planer and Laminate Decks is crucial for safe and efficient operation. Below is an overview of these components and their functions:
High-Speed Planer
The High-Speed Planer is a sophisticated machine designed to dress laminates by trimming and shaping them on all four sides, ensuring uniform thickness and smooth surfaces. It operates at high speeds (up to 80 meters per minute), using multiple cutter heads to precisely shape the laminates before they move on to the glue applicator and press.
- Cutter Heads: The HSP uses five cutter heads positioned on the top, bottom, and sides of the timber. These cutter heads can be adjusted to meet the required width and thickness of the laminate.
- Feed Rollers: These rollers guide the timber laminates through the planer. They apply consistent pressure to ensure that the timber feeds evenly through the cutting area.
- Planer Bed and Sound/Safety Hood: The planer bed supports the laminates during the trimming process, while the sound/safety hood reduces noise levels and protects operators from flying debris. The hood must be closed during operation.
- Bed Lubricant System: This system ensures that the planer bed remains lubricated, preventing jams and damage to the timber during the feeding process.
- Dust Extraction System: The planer is equipped with a dust extraction system to remove shavings and maintain a clean working environment, essential for the longevity of the machine and the quality of the product.