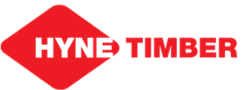
HIGH SPEED PLANER (HSP)
Post-Operational Checks
Introduction
The post-operational checks ensure that the High-Speed Planer (HSP) is safely shut down, cleaned, and prepared for the next shift. These checks help to maintain the machine’s performance, extend its lifespan, and ensure that the working area is safe and organized. By completing these steps, operators can prevent future operational issues and ensure the machine is ready for the next production cycle.
Procedure for Post-Operational Checks
At the end of each shift, the operator must perform the following checks to ensure the HSP section is safely and properly shut down. If any issues arise during the checks, the operator must note them in the comments section and report them for follow-up action.
Step 1: Turn Off the HSP and Open the Door
- Post-Operational Check Item: TURN OFF HSP & OPEN DOOR
- Description: Safely power down the HSP using the HMI (Human-Machine Interface) and ensure that all moving parts have come to a complete stop. Once the machine is off, open the safety door to begin the cleaning process.
- Action: Use the control panel to turn off the HSP and open the door for cleaning access.
Step 2: Clean/Blow Down the HSP
- Post-Operational Check Item: CLEAN/BLOW DOWN HSP
- Description: Use compressed air to blow down the HSP, removing sawdust, debris, and any loose materials from inside the machine. This helps to prevent buildup that could cause issues during the next operation.
- Action: Thoroughly clean the machine using the appropriate cleaning tools and blowers.
Step 3: Remove Outriggers and Collars
- Post-Operational Check Item: REMOVE OUT-RIGGERS & COLLARS
- Description: Safely remove the outriggers and collars that were installed during the operation. Ensure these components are properly stored in their designated locations for the next shift.
- Action: Remove and store outriggers and collars.
Step 4: Keep the Door Open on the HSP
- Post-Operational Check Item: KEEP DOOR OPEN ON HSP
- Description: Leave the HSP door open after cleaning to allow proper ventilation and drying if necessary.
- Action: Ensure the door remains open after cleaning is completed.
Step 5: Clean the FJ Press Area
- Post-Operational Check Item: CLEAN FJ PRESS AREA – REMOVE TIMBER SCRAP & SPRAY
- Description: Clean the finger jointer (FJ) press area by removing any timber scraps and spraying down the work surface to ensure it is ready for the next shift.
- Action: Remove timber scraps and clean the area with appropriate sprays.
Step 6: Remove Damaged/Marked Lams from the Deck
- Post-Operational Check Item: REMOVE ANY DAMAGED X MARKED LAMS FROM DECK & CUT UP
- Description: Identify and remove any damaged or marked laminates (lams) from the deck. These should be cut up or disposed of properly to prevent them from being used in the next production cycle.
- Action: Remove and process damaged laminates.
Step 7: Clean Up All Timber from Saw Horses and Trolleys
- Post-Operational Check Item: CLEAN UP ALL TIMBER FROM SAW HORSES/TROLLEYS
- Description: Clear away any remaining timber from saw horses and trolleys. Ensure that the area is free of clutter to prevent accidents and ensure a smooth start for the next shift.
- Action: Remove all timber from the area and store it properly.
Step 8: Clean the Floor Area of the HSP Work Area
- Post-Operational Check Item: CLEAN FLOOR AREA OF HSP WORK AREA – ENSURE TRIP HAZZARDS REMOVED
- Description: Sweep and clean the floor area surrounding the HSP to remove any debris, timber, or materials that could pose a trip hazard.
- Action: Sweep and remove all trip hazards from the area.
Step 9: Add Total Lineal Meters on the Board
- Post-Operational Check Item: ADD TOTAL L/M ON BOARD FOR WOOD MACHINIST
- Description: Record the total lineal meters (L/M) processed during the shift on the board for the wood machinist to review.
- Action: Add the correct data to the board.
Step 10: Close the HMI Cover
- Post-Operational Check Item: CLOSE HMI COVER TO PROTECT SCREEN
- Description: Close the HMI cover to protect the screen from dust, debris, and accidental damage.
- Action: Securely close the cover over the HMI.
Step 11: Clean the Work Centre Table
- Post-Operational Check Item: CLEAN OFF WORK CENTRE TABLE READY FOR NEXT DAY
- Description: Clean off the work center table, removing any tools, paperwork, or debris. Make sure it is organized and ready for the next operator to begin their shift.
- Action: Clear and organize the table.
Step 12: Complete Downtime Paperwork and Fill Out MBU Board
- Post-Operational Check Item: COMPLETE DOWNTIME PAPERWORK & FILL OUT MBU BOARD
- Description: Ensure that all downtime paperwork is filled out accurately and recorded on the MBU board for future review.
- Action: Complete the necessary paperwork and update the MBU board.
Step 13: Ensure Fans and UV Light Are Off
- Post-Operational Check Item: ENSURE FANS & UV LIGHT IS OFF
- Description: Check that all fans and UV lights are turned off to conserve energy and prevent unnecessary wear.
- Action: Turn off any fans and UV lights.
Step 14: Check Cleaning Equipment
- Post-Operational Check Item: ENSURE ALL CLEANING EQUIPMENT IS FULL & IN CORRECT STORAGE AREA FOR NEXT USE
- Description: Check that all cleaning supplies (e.g., sprays, cloths) are refilled, stored correctly, and ready for the next shift.
- Action: Refill and store cleaning equipment as necessary.
Final Step: Report Maintenance Issues
- Post-Operational Check Item: REPORT ANY NOTIFIABLE MAINTENANCE OR WEAR & TEAR
- Description: If you notice any maintenance issues or signs of wear and tear, report them immediately to the maintenance team for follow-up.
- Action: Document any issues and inform the maintenance team.
By following these post-operational checks, operators ensure that the HSP and its surrounding area are clean, safe, and ready for the next shift. This prevents machine wear, ensures safety, and maintains efficient production for the next operating cycle.
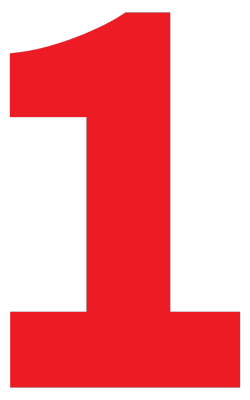
Clean the Paperwork Area
-
- Task: Clean the Paperwork Area
- Description: Ensure that the paperwork and printer area are free from clutter and dust. A clean and organized workspace helps ensure that documents are accessible and prevents any misplacement of important records.
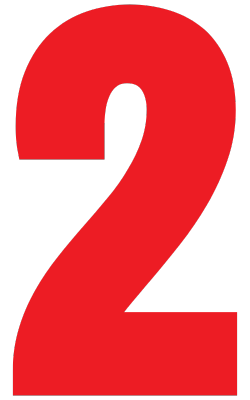
File Daily Paperwork
- Task: Place Daily Paperwork in Tray
- Description: File all job sheets and paperwork from the day into the designated tray. Proper filing ensures that records are easily retrievable for future reference.
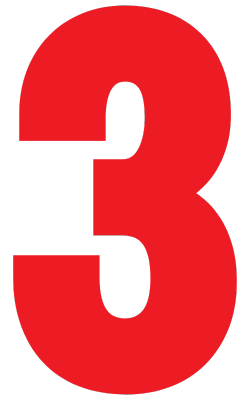
Charge Crane Remotes and Saw Battery
- Task: Put Crane Remotes and Saw Battery on Charge:
- Description: Ensure that all crane remotes and the dunnage saw battery are placed on charge for the next shift. Fully charged equipment prevents delays in operations.
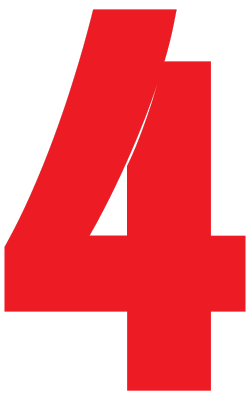
Clean the Finger Jointer (FJ) Press Area
- Task: Clean the FJ Press Area
- Description: Remove any timber scraps, debris, and spray residue from the Finger Jointer press area. A clean press area prevents buildup that could interfere with operations and cause wear on machinery.
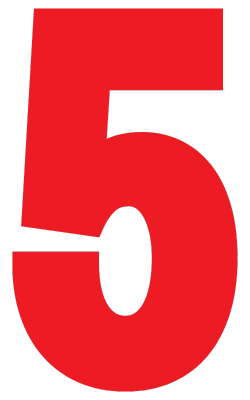
Check and Record Container Levels
- Task: Check Container Levels and Record on Whiteboard:
- Description: Remove any glue residue from the rollers and apply glue release to keep them in good condition.
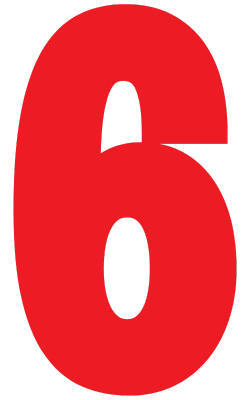
Communicate Full Container Status
- Task: Text RMK Levels and Disconnect Full Containers:
- Description:If any containers are full, text Russell or the waste removal team (RMK) to inform them of the levels. Disconnect full containers to prevent overfilling and ensure timely waste removal.
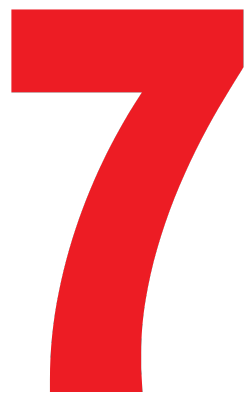
Clean Dunnage Area
- Task: Clean Dunnage Area of Rubbish and Sawdust:
- Description: Remove any rubbish, sawdust, and debris from the dunnage area. A clean area ensures safe and efficient access to materials during the next shift.
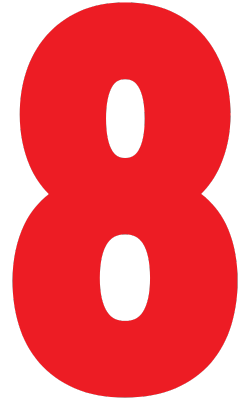
Assist in Cleaning the FJ and Dance Floor Areas
- Task: Assist in Cleaning FJ and Dance Floor Areas:
- Description: Collaborate with other team members to clean the Finger Jointer and Dance Floor areas. This includes sweeping, removing debris, and wiping down surfaces. A well-maintained area reduces wear on machinery and ensures a safe workspace.
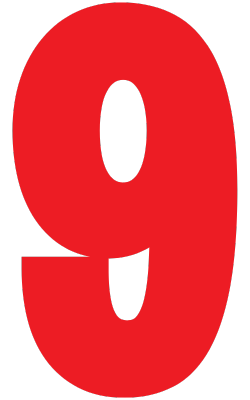
Ensure Smoko Room is Properly Shut Down
- Task: Ensure Smoko Room Aircons and Lights are Off & Door is Shut:
- Description: Check that all air conditioning units and lights in the Smoko room (break area) are turned off. Make sure the door is closed to prevent energy waste and unauthorized access.
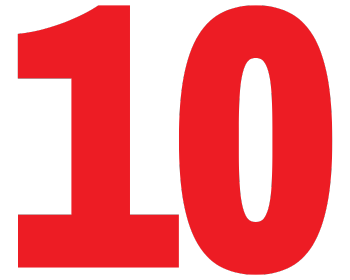
Turn Off the Outfeed Fan
- Task: Turn Off Outfeed Fan
- Description: Work with the team to ensure these areas are also clean and ready for the next shift.
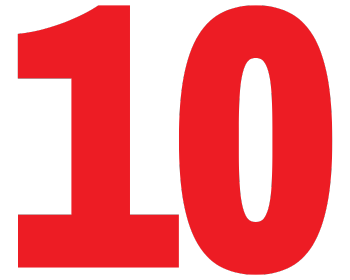
Double Check D-Zone Outfeed HMI
- Task: Ensure D-Zone Outfeed HMI is Off and Screen Cover Down:
- Description: Verify that the Human-Machine Interface (HMI) screen in the D-Zone is turned off and that the cover is down. This prevents unnecessary power usage and protects the screen from dust or damage.
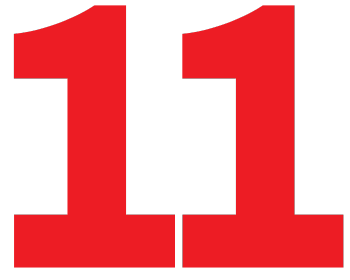
Prepare Cleaning Equipment for Next Use
- Task: Ensure Cleaning Equipment is Full and Properly Stored:
- Description: Check that all cleaning tools (brooms, scrapers, etc.) are in good condition, stored properly, and ready for use during the next shift. Refill any supplies (e.g., cleaning agents) as needed to avoid delays in cleaning tasks.
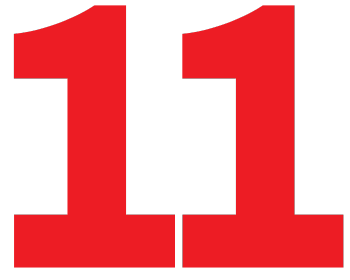
Prepare Cleaning Equipment for Next Use
- Task: Ensure Cleaning Equipment is Full and Properly Stored:
- Description: Check that all cleaning tools (brooms, scrapers, etc.) are in good condition, stored properly, and ready for use during the next shift. Refill any supplies (e.g., cleaning agents) as needed to avoid delays in cleaning tasks.
Reporting and Recording Issues
Record Maintenance Needs: If any wear and tear, damage, or other maintenance issues are noticed during the checks, they must be recorded in the designated section of the shutdown form. This ensures that maintenance staff can address the issues before the equipment is used again.
Well Done!
-
After completing all post-operational checks, the operator must sign off on the checklist to confirm that all tasks have been completed to standard. This sign-off ensures accountability and helps maintain safety and efficiency in the Outfeed section.